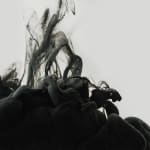
Sadza (kopeć, za encyklopedią PWN) - w przenośni, a można rzec i dosłownie, Kopciuszek w porównaniu z bardziej "medialnymi" odmianami węgla pierwiastkowego takimi jak fulereny czy grafen, a już na pewno z najcenniejszymi kamieniami szlachetnymi - diamentami. Jest produktem niepełnego spalania paliw kopalnych, jak również materiałów zawierających znaczne ilości węgla. Sadza techniczna składa się niemal wyłącznie z węgla pierwiastkowego (>97%), w przeciwieństwie do sadzy kominowej czy tej powstającej w czasie pożarów, które zawierają mniej niż 60% węgla pierwiastkowego oraz duże ilości zanieczyszczeń nieorganicznych i wielopierścieniowych węglowodorów aromatycznych (WWA).
Sadza była znana ludziom pierwotnym w czasach prehistorycznych. Wykorzystywali ją jako jeden z pigmentów, obok żółtej i czerwonej ochry, do tworzenia malowideł naskalnych. Wraz z rozwojem pisma, w różnych kulturach zaczęto jej używać do wyrobu tuszu. I tak przykładowo, w starożytnym Egipcie wytwarzano go z sadzy powstającej po wypaleniu kaganka, zmieszanej z wodą i gumą arabską (podobno znaki zapisane nim na papirusie ok. 3000 lat p.n.e. są czytelne do dziś). W tym samym okresie, w odległych Chinach, sadzę i tusz do kaligrafii produkowano już w ogromnych ilościach, w sposób zorganizowany. Rzemieślnicy zeskrobywali sadzę gromadzącą się na ceramicznych pokrywach lamp olejowych i mieszali ją z klejem zwierzęcym i pachnidłem. Podobną metodą do dzisiaj wytwarzany jest tradycyjny japoński tusz zwany sumi, sprzedawany w postaci pałeczek. Ze względu na jakość wykorzystywanych surowców oraz czasochłonną technikę, dwustugramowy produkt może osiągać cenę nawet 2000 dolarów. Jeśli znajdą się czytelnicy chętni do zapoznania się ze szczegółami wspomnianego procesu, zachęcam do obejrzenia filmu Why Japanese Calligraphy Ink Is So Expensive w serwisie YouTube na kanale Business Insider. Podobno obraz jest wart więcej niż tysiąc słów. Ogólna receptura, według której wytwarzano większość tuszów, nie zmieniła się do XIX w.
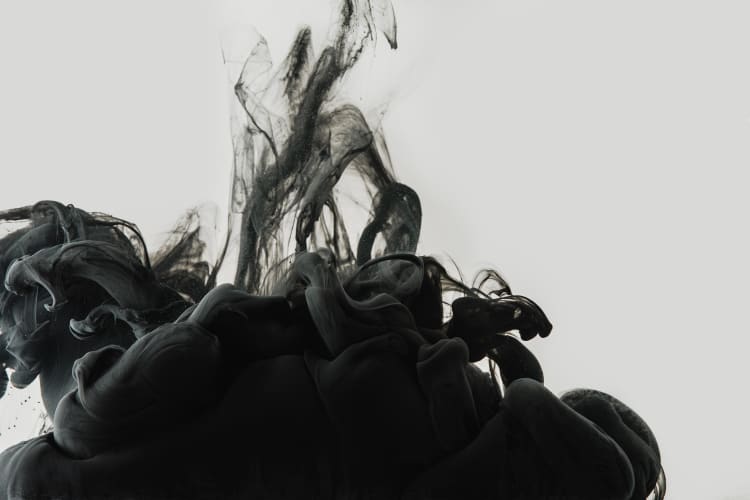
Do roku 1870 sadzę wytwarzano przeważnie metodą lampową; później zaczęto do tego celu wykorzystywać gaz ziemny. Opracowano proces kanałowy, w którym gaz spalano przy ograniczonym dopływie powietrza w niskich, metalowych instalacjach kojarzących się z psimi budami (ang. doghouses). Wydajność procesu była niska; wynosiła jedynie kilka procent, po części przez kwestie surowcowe, a przede wszystkim ze względu na bardzo niską skuteczność wychwytywania powstającej sadzy. Nad fabrykami pracującymi według tej metody unosiły się czarne smugi produktu widoczne z odległości dziesiątek kilometrów. Patrząc na obowiązujące obecnie przepisy środowiskowe i podejście do ekologii, aż dziw bierze, że ostatnią tego typu wytwórnię zamknięto w Stanach Zjednoczonych dopiero w 1976 r.
W 1904 r. Sidney C. Mote odkrył, że dodatek sadzy poprawia właściwości fizykochemiczne wyrobów gumowych, co stanowi najbardziej istotne wydarzenie w historii rozwoju przemysłu sadzy technicznej. Wiedza ta została wykorzystana w rozwijającym się przemyśle motoryzacyjnym do wyrobu opon.
Szybki rozwój motoryzacji oraz wprowadzenie na rynek kauczuków syntetycznych doprowadziły do szeroko zakrojonych prac badawczo-rozwojowych związanych z napełniaczami sadzowymi. Na początku XX w. wprowadzono dwie inne metody, obie wykorzystujące gaz ziemny jako surowiec, ale zapewniające lepszą wydajność i niższe emisje zanieczyszczeń niż proces kanałowy. Jedną z nich jest stosowany do dzisiaj tzw. proces termiczny, w którym gaz ziemny podawany jest do gorącego pieca wyłożonego materiałem ogniotrwałym, gdzie w warunkach beztlenowych, w podwyższonej temperaturze, ulega pirolizie z wydzieleniem sadzy, mieszaniny związków organicznych i wodoru. Zazwyczaj stosuje się układ 2 reaktorów pracujących naprzemiennie. Gaz wylotowy z pierwszego reaktora schładza się za pomocą natrysków wodnych, a sadzę zbiera się na filtrach tkaninowych. Przefiltrowany gaz (90% wodoru, 6% metanu, 4% wyższych węglowodorów) służy do ogrzania drugiego reaktora. Drugą ze wspomnianych metod był gazowy proces piecowy, który nie jest już praktykowany.
Obecnie najczęściej wytwarza się sadze techniczne metodą olejowo-piecową (lub po prostu piecową), którą wprowadziła firma Philips Petroleum w 1943 r. W procesie tym wykorzystuje się ciężkie oleje aromatyczne. Reakcje zachodzą w reaktorze, w ściśle kontrolowanych warunkach (temperaturze i ciśnieniu). Surowiec za pomocą dysz atomizujących wprowadzany jest do strumienia gorącego gazu, w którym odparowuje i ulega pirolizie. Produkt usuwany jest z reaktora poprzez wymienniki ciepła, chłodzony i gromadzony w filtrach workowych. Odfiltrowana sadza jest granulowana, suszona, przesiewana i przygotowywana do transportu.
Po dziś branża motoryzacyjna zużywa najwięcej sadzy technicznej. Ze względu na fakt, że sadza jest odporna na promieniowanie ultrafioletowe i działa jako pochłaniacz ozonu, a więc nie tylko z powodu koloru, jest ona również najpowszechniej stosowanym czarnym pigmentem w przetwórstwie tworzyw sztucznych oraz do wyrobu farb i tuszów. Globalny popyt na sadzę techniczną przekracza 16 mln ton rocznie.