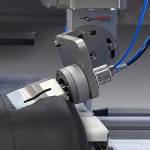
Technologie cięcia ultradźwiękowego są stosowane do cięcia gumy opon od dziesięcioleci, ponieważ technologia ta umożliwia uzyskanie nieskazitelnych krawędzi cięcia przy zachowaniu niskiego poziomu zużycia energii. Jednakże dotąd dużym problemem było tempo zużycia ultradźwiękowych sonotrod używanych jako narzędzia tnące. Ciepło generowane w tym procesie powodowało, że musiały być one często wymieniane, nawet po kilku tygodniach. Zużycie spowodowane procesem cięcia skutkowało również gromadzeniem się fragmentów na sonotrodzie, które następnie musiały być mozolnie usuwane ręcznie. To czyszczenie, w połączeniu z częstą wymianą sonotrod, prowadziło do dłuższych przestojów w procesie produkcyjnym.
Dzięki nowemu materiałowi i inteligentnej konstrukcji narzędzia tnącego firma Herrmann Ultraschalltechnik GmbH & Co. KG ma do zaoferowania nowe rozwiązanie. Opracowana na nowo sonotroda wykonana ze specjalnej hartowanej stali umożliwia precyzyjne, czyste cięcia i ma dłuższą żywotność niż konwencjonalne narzędzia tnące. Dzięki połączeniu z solidnymi konwerterami ultradźwiękowymi i generatorami oraz ciągłemu monitorowaniu procesu firma Herrmann była w stanie zoptymalizować cały proces cięcia ultradźwiękowego. To nie tylko obniża koszty konserwacji, ale także skraca czas przestojów w operacjach produkcyjnych.
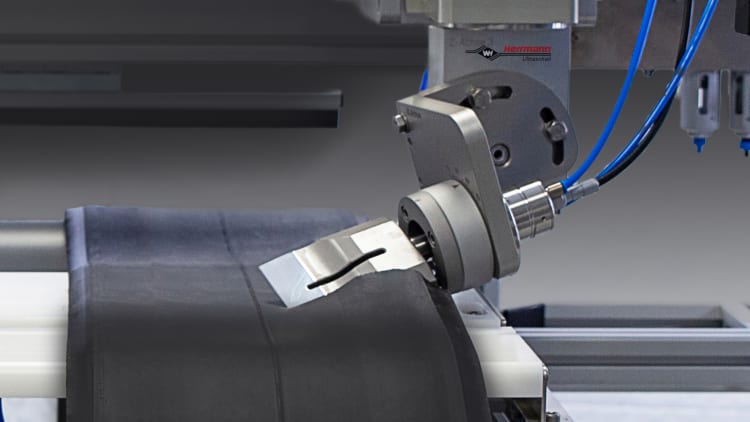
Pięciokrotnie dłuższa żywotność niż w przypadku sonotrod stalowych.
Do tej pory sonotrody były w większości wykonane z aluminium lub tytanu. Aluminium nie ma odpowiedniej twardości do długotrwałego użytkowania. Tytan jest twardszy, ale magazynuje ciepło z procesu cięcia. Wpływa to nie tylko na wytrzymałość tytanowej sonotrody, ale także prowadzi do przeniesienia części ciepła na gumę. Oznacza to, że cząsteczki zanieczyszczeń przywierają do niej, co z kolei pogarsza rezultat cięcia. W konsekwencji operacje produkcyjne muszą zostać zatrzymane, a sonotrody muszą zostać wyczyszczone ręcznie.
Podczas opracowywania trwałego narzędzia tnącego przekonaliśmy się, że specjalny stop stali ma najlepsze właściwości materiałowe. Ma większą twardość niż tytan i można na nim polegać pod względem rozpraszania generowanego ciepła. Oznacza to, że sonotroda w dużej mierze pozostaje zimna podczas procesu cięcia i zapewnia czyste cięcie. Jednocześnie jest chroniona przed przywieraniem fragmentów gumy, co eliminuje potrzebę czasochłonnego czyszczenia.
Oprócz materiału kluczowe znaczenie ma także geometria sonotrody. Ogólna zasada jest taka: im cieńsza sonotroda, tym lepsza krawędź cięcia. Jeśli jest zbyt cienka, jej wytrzymałość będzie gorsza. Wyraźnie widać przewagę tego hartowanego stopu stali, ponieważ nawet przy cieńszych cięciach sonotroda nie pęka i pozostaje ostra, także przy ciągłym użytkowaniu. Dzięki temu sonotrody stalowe mogą być używane do pięciu razy dłużej niż sonotrody konwencjonalne.
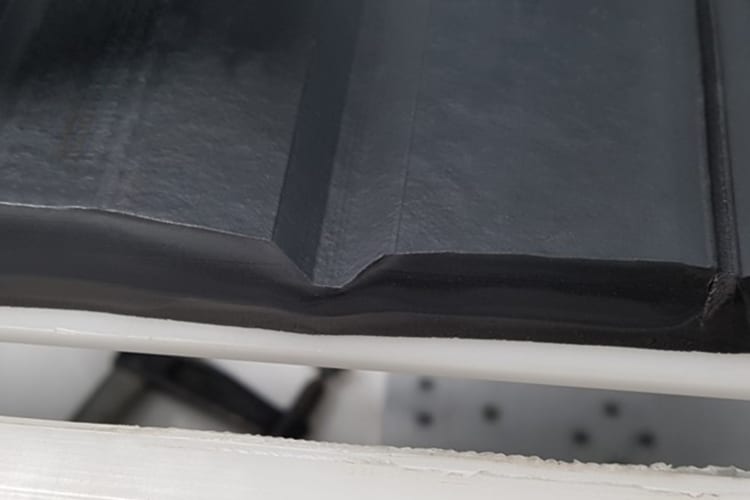
Niezawodny konwerter dzięki bogatemu doświadczeniu
Podobnie jak sonotroda, konwerter ultradźwiękowy odgrywa ważną rolę. Podczas całego procesu cięcia musi on przekształcać drgania elektryczne generatora w drgania mechaniczne w sposób niezawodny i powtarzalny. Stosowanie tanich materiałów i wysokich zakresów częstotliwości, które również powodują powstawanie szkodliwych częstotliwości bocznych, negatywnie wpływa na trwałość konwerterów. Ulegają one awariom i muszą być regularnie wymieniane – jest to kolejny czynnik, który prowadzi do przestojów w produkcji.
Bogate doświadczenie w zakresie ultradźwięków nauczyło firmę Herrmann, że tych przestojów można uniknąć, produkując cały konwerter z tytanu, a nie częściowo z części aluminiowych, jak to było wcześniej. Przekonaliśmy się, że tytan jest bardziej wytrzymały, a tym samym bardziej trwały, przede wszystkim w przypadku ciągłego użytkowania. Ponadto tytan może przenosić ultradźwięki lepiej niż aluminium pod względem akustycznym, co zapobiega występowaniu zakłócających częstotliwości bocznych.
Monitorowanie procesu za pomocą inteligentnego generatora
Generator ultradźwięków wytwarza niezbędne oscylacje elektryczne dla konwertera. Oprócz kontrolowania procesu cięcia zajmuje się również monitorowaniem. Dane każdego procesu mogą być eksportowane i oceniane. Ponadto w generatorze można zapisać idealne parametry procesu cięcia, co oznacza, że cały system jest szybko gotowy do ponownego użycia po wymianie komponentu. Producenci uzyskują najlepsze wyniki, gdy generator, konwerter i sonotroda są ze sobą kompatybilne od samego początku. Zapobiega to wibracjom i znacznie wydłuża żywotność poszczególnych komponentów. Laboratorium ultradźwiękowe firmy Herrmann wspiera klientów w analizie procesu i określaniu idealnych parametrów procesu cięcia.
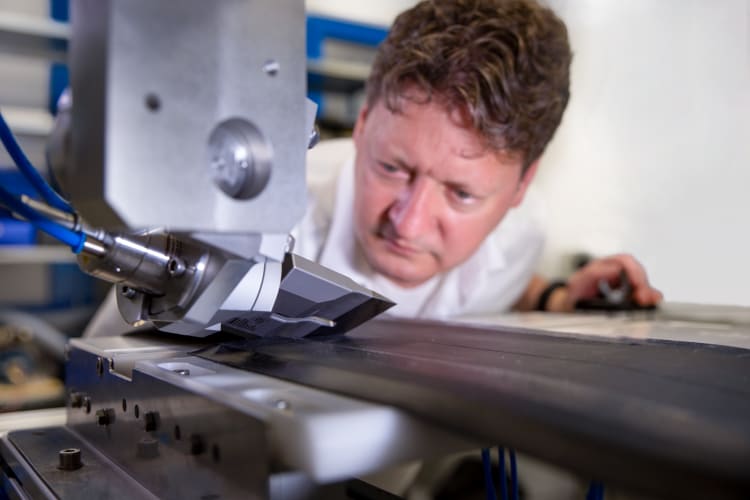
Łatwa integracja dostępna na całym świecie
Za pomocą ultradźwięków można precyzyjnie ciąć gumę o różnej grubości i składzie, uzyskując spójne wyniki. Technologia ta jest wykorzystywana głównie w produkcji opon do pojazdów osobowych i może być łatwo zintegrowana z istniejącymi liniami produkcyjnymi. Wprowadzając lub optymalizując systemy ultradźwiękowe, firma Herrmann służy pomocą jako partner w dowolnym miejscu na świecie i doradza firmom, w jaki sposób mogą czerpać korzyści z tej energooszczędnej i niezawodnej technologii cięcia. W tym celu komponenty mogą być testowane przez kilka miesięcy we własnych systemach produkcyjnych.