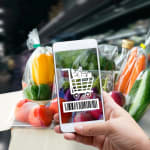
Produkcja opakowań stanowi ważny segment branży poligraficznej. W wyniku zmian technologicznych drukowanie staje się jednym z etapów procesu produkcyjnego opakowania. Dlatego też coraz częściej drukarnie opakowaniowe przekształcają się w producentów opakowań - ocenia się, że udział poligrafii opakowaniowej w krajowym rynku poligraficznym sięga ok. 50%.
Rola opakowań zmieniła się na przestrzeni ostatnich lat. Choć nadal ich zadaniem jest ochrona towarów przed wpływem czynników środowiskowych, to równocześnie pełnią one rolę niemego sprzedawcy. Poprzez oryginalną formę, dobór materiałów, barw i grafik opakowania pozwalają tworzyć określony wizerunek firmy, wyróżniają dany produkt spośród gamy podobnych wyrobów, przyciągają uwagę klienta.
Nowe rozwiązania cyfrowe i miniaturyzacja układów scalonych umożliwiły projektantom opakowań i przetwórcom realizować pomysły, które wcześniej nie były możliwe. Rozwija się technologia elektroniki drukowanej (printed electronics), w której standardowe techniki druku wykorzystuje się do wykonywania ścieżek przewodzących na sztywnym lub elastycznym podłożu - tekturze, papierze, foliach polimerowych. Kiedy opakowania stają się fizycznym nośnikiem informacji w formie drukowanej jak i cyfrowej, wówczas określamy je mianem „inteligentnych”.
Choć jak dotychczas skala wykorzystania opakowań inteligentnych jest mocno ograniczona, to przewiduje się, że w niedalekiej przyszłości coraz więcej produktów będzie miało opakowania z elementami elektronicznymi nanoszonymi metodami drukarskimi. Szacuje się, że w latach 2020-2030 skumulowany wskaźnik wzrostu w dziedzinie elektroniki drukowanej wyniesie 22,4%, a przychody z rynku przekroczą wartość 363 mld dolarów.
Zastosowanie tradycyjnych technik drukarskich oraz technik cyfrowych do wytwarzania elastycznej elektroniki jest ekonomicznie opłacalne i nie wymaga dodatkowych nakładów inwestycyjnych, ani też zachowania specjalnych warunków produkcyjnych. Ponadto, techniki te otwierają możliwość drukowania ze zwoju na zwój oraz na dużych powierzchniach. Pozwala to w prosty sposób rozszerzyć funkcjonalność opakowań na masową skalę w zakresie:
- monitorowania jakości produktów
- poprawy wygody użytkowania (interakcji z interfejsami urządzeń elektronicznych)
- kontroli łańcucha dostaw oraz bezpieczeństwa i identyfikacji produktu.
Obecnie największą barierę dla tej technologii stanowi proces wytwarzania układów scalonych, niezbędnych do przekazywania informacji drogą radiową, ze względu na niemożliwą do osiągnięcia technikami drukarskimi rozdzielczość. W tym obszarze technologie są nadal w fazie badań i testów. Dlatego jedynym rozwiązaniem są systemy hybrydowe, znane pod nazwą „zintegrowanych systemów inteligentnych” (Integrated Smart Systems). W praktyce na etykiecie lub opakowaniu drukowane są obwody i elementy elektroniczne - czujniki, siłowniki, anteny - w zakresie na jaki pozwala rozdzielczość druku przemysłowego, a następnie są w nie wmontowywane mikroczipy wytwarzane metodami tradycyjnymi.
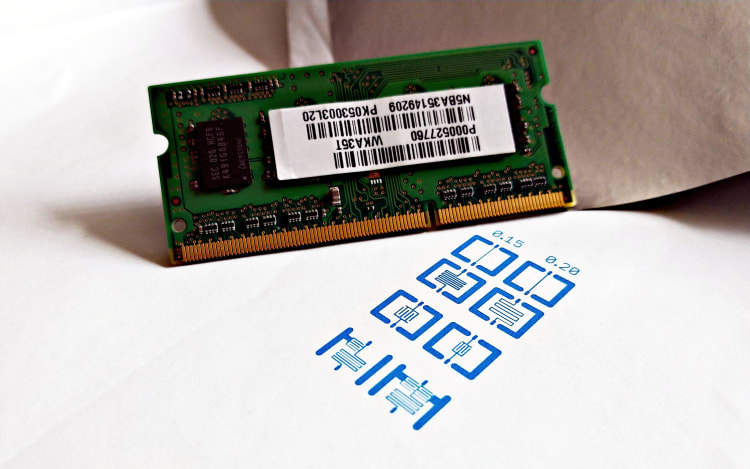
Fot. 1. Elektronika tradycyjna, a elektronika drukowana
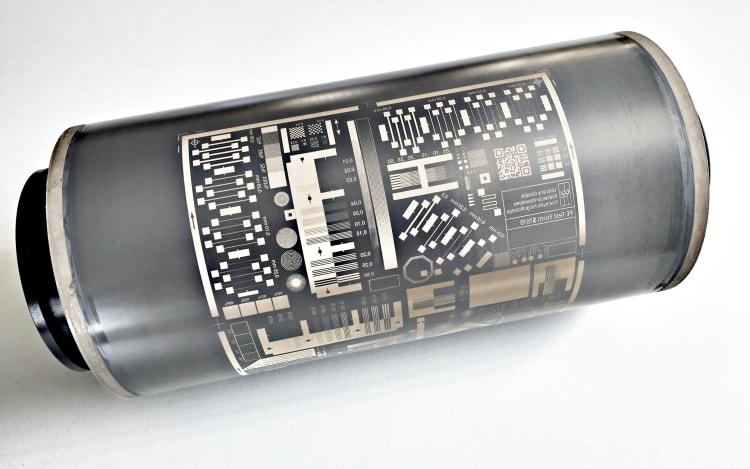
Fot. 2. Testowa forma do sitodruku rotacyjnego
O procesie produkcji w dużym skrócie
Wytwarzanie tradycyjnej elektroniki wymaga przeprowadzenia szeregu operacji w celu wykonania ścieżek przewodzących na określonym typie podłoża (np. na płytce półprzewodnikowej do układów scalonych). Podstawowym, wywodzącym się z technologii półprzewodnikowej procesem wykorzystywanym w produkcji jest fotolitografia. Składają się na niego następujące etapy:
- przygotowanie powierzchni (odtłuszczenie i wygrzanie)
- nałożenie emulsji światłoczułej
- wygrzewanie emulsji
- naświetlanie promieniowaniem ultrafioletowym płytki pokrytej emulsją z przyłożoną fotomaską
- wywoływanie (usunięcie części emulsji)
- trawienie podłoża lub tworzenie dodatkowych warstw np. metalicznych lub tlenkowych
- usunięcie pozostałości emulsji z powierzchni płytki.
W przeciwieństwie do procesu fotolitograficznego, tworzenie struktur materiałowych na podłożach za pomocą technik jest prostym, dwuetapowym procesem. Materiały przewodzące, w postaci farby drukarskiej bądź pasty, osadzane są bezpośrednio na podłożu, od razu w wybranych obszarach. Po wydrukowaniu konieczna jest zazwyczaj odpowiednia obróbka termiczna, aby doprowadzić materiał do druku do stanu użytkowego. W tej fazie produkcji następuje odparowanie rozpuszczalników oraz spiekanie i utwardzanie pigmentów i innych składników znajdujących się w farbie, co poprawia przewodnictwo.
Do wytwarzania elektroniki drukowanej stosuje się kilka dobrze znanych technik drukarskich, które można podzielić na klasyczne - wymagające zastosowania formy drukowej (m.in. fleksografia, sitodruk, rotograwiura, tampondruk) oraz cyfrowe - bezkontaktowe, niewymagające stosowania form (np. inkjet).
Farby przewodzące
Jako składniki farb przewodzących do produkcji elektroniki drukowanej przebadano wiele różnych substancji. Stosuje się je w postaci zawiesiny funkcjonalnej w roztworach żywic organicznych utrwalanych za pomocą temperatury bądź promieniowania UV. W warstwach przewodzących mogą to być proszki metali w skali mikronowej - głównie srebra, miedzi i aluminium, polimery przewodzące lub związki metaloorganiczne. W warstwach rezystywnych grafit, sadza, nanorurki węglowe. Z kolei w warstwach dielektrycznych i izolacyjnych - tytanian baru, dwutlenek tytanu, szkliwa.
Stwierdzono, że polimery przewodzące sprawdzają się w urządzeniach aktywnych, takich jak organiczne diody elektroluminescencyjne i fotodiody, baterie, czujniki. Do elementów pasywnych - anten sensorów - zwykle stosuje się farby, które zawierają cząstki metaliczne.
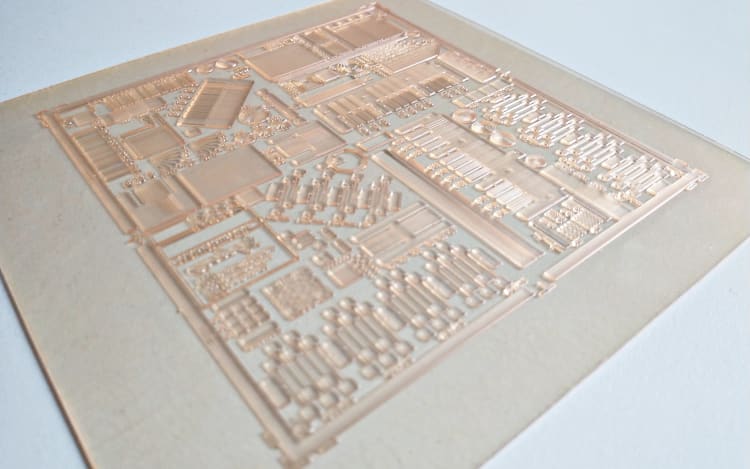
Fot. 3. Testowa forma fleksograficzna
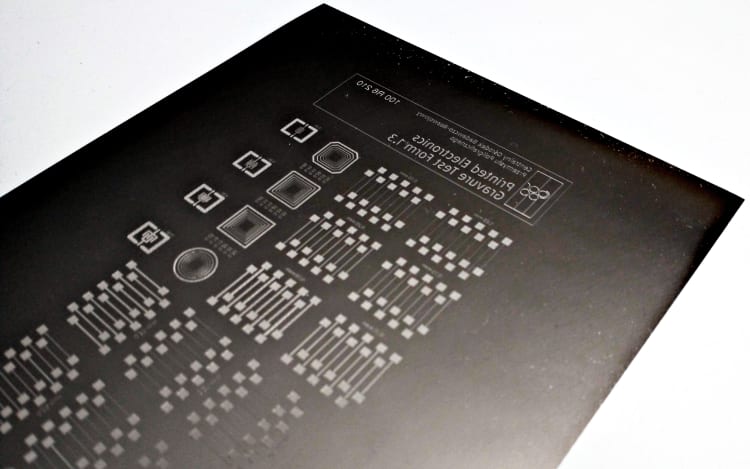
Fot. 4. Testowa forma do wklęsłodruku (rotograwiury)
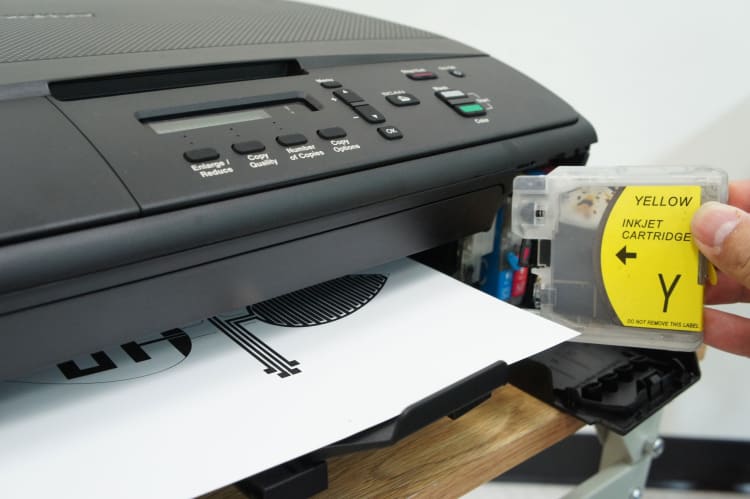
Fot. 5. Prototypowanie obwodu z wykorzystaniem drukarki atramentowej – standardowy wkład napełniony jest tuszem z nanocząsteczkami srebra (źródło: https://www.news.gatech.edu/
Podłoża
Właściwości podłoża - reologia, energia powierzchniowa - odgrywają znaczącą rolę w technologii elektroniki drukowanej przy projektowaniu układów. Od kompatybilności podłoża i farby/atramentu zależy, czy dany produkt można wyprodukować, czy nie.
Można drukować m.in. na szkle, papierze, polimerach. Wyzwaniem przy drukowaniu na szkle jest mała chropowatość powierzchni. Podłoża papierowe cieszą się coraz większą popularnością jako materiały bazowe dla elektroniki dru-kowanej, głównie ze względu na dostępność i niskie koszty. Bez większych problemów można wykonywać na nich nadruki, jednak wyzwaniem jest ich duża porowatość, która ułatwia migrację aktywnych mikrocząstek do głębszych warstw, powodując spadek przewodności.
Najczęściej stosowanymi podłożami elastycznymi są polimery - poliamid, politereftalan etylenu (PET) i polietylenonaftalan (PEN). Znaczenie zyskują również biomateriały ze względu na biokompatybilność i biodegradowalność, co może być przydatne w zastosowaniach medycznych.