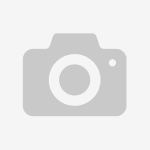
Projekt Hasco opierał się na wykorzystaniu specjalnych technologii produkcji oraz konstrukcji, a także technologii gorących kanałów. Nowa forma była wykonywana na potrzeby jednego z największych światowych producentów dozowników rozpylających i pojemników do cieczy przeznaczonych dla branży sanitarnej i kosmetycznej.
Zadaniem, stojącym przed technologami Hasco było zwiększenie wydajności już pracujących form, tak aby zredukować koszty wytwarzania dozowników rozpylających. Zamiar się udał i doprowadzono do wzrostu wydajności konwencjonalnej formy trzypłytowej. Uzyskanie takiego stanu polegało na modyfikacji układu zimnych kanałów wtryskowych (zimny wtrysk) na układ wtrysku GK. Ma to związek przede wszystkim z tym, że czas chłodzenia kanałów wtryskowych zajmuje największą część całego procesu chłodzenia. Wpływa też dominująco na czas całego cyklu pracy formy.
Innowacja ze strony Hasco polegała na zlikwidowaniu drugiej linii podziału i jednocześnie zastosowaniu układu GK, co przyspieszyło otwieranie i zamykanie formy. Dzięki temu możliwe stało się również uniknięcie wysokich kosztów wypychania wlewka i recyklingu przetworzonego tworzywa sztucznego. Istniejące formy zostały dokładnie przeanalizowane, a następnie ustalono możliwe dla technologii GK punkty wtrysku.
W celu uzyskania jak najlepszego punktu wtrysku trzeba było dokonać zmiany konstrukcji detali. By to osiągnąć wykonany został kompletny projekt 3D modyfikacji w środowisku Unigraphics. Programy CNC służące do modyfikacji wkładek formujących, a także do produkcji potrzebnych elektrod zostały wygenerowane automatycznie. Wkładki formujące zostały ponownie spasowane, zoptymalizowano system ich chłodzenia oraz wyprodukowano nową płytę oporową.
Podczas wyboru odpowiedniej dyszy GK HASCO zdecydowano się sięgnąć po nową wersję dyszy Z33/... z torpedą z brązu berylowego o wymiarach 25x63 mm. Tego rodzaju dysza zapewnia optymalne przewodzenie ciepła w obrębie przewężki przy jednoczesnym zachowaniu kompaktowej konstrukcji. Przetwarzanym materiałem był w tym wypadku polipropylen.
Kolejnym wyzwaniem, stojącym przed technologami Hasco było takie umieszczenie punktu wtrysku - możliwie jak najmniejszego - by nie robiły się jakiekolwiek smugi i możliwa była również jak najszybsza zmiana koloru. Oba te oczekiwania zostały optymalnie spełnione przez wspomnianą dyszę Z33201/ 25x63 mm. Oba systemy zostały zaprojektowane w tym przypadku jako kompletne gorące połówki. Dla korpusu rozpylacza zastosowano 32 dysze, a dla dźwigni 12. W układzie dla dźwigni poprzez krótkie zimne kanały i cztery punkty wtrysku uzyskano łącznie 48 detali.
Rezultat projektu: skrócenie czasu cyklu o 30 proc., oznaczające znaczny wzrost wydajności produkcji.