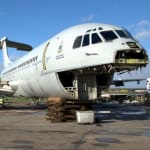
Tym niemniej wciąż pozostaje wyzwaniem kwestia recyklingu materiałów kompozytowych, których naczelna cecha - wysoka trwałość - staje się w tym przypadku problemem. Badania w tym kierunku zostały podjęte w Europie w latach 80. XX wieku, między innymi przez zespół prof. Andrzeja Błędzkiego pracującego wówczas na Uniwersytecie w Kassel (Niemcy).
Najpoważniejszym przedsięwzięciem w zakresie przemysłowego recyklingu kompozytów SMC była w latach 90. XX wieku działalność firmy ERCOM, wspólnej inicjatywy firm BASF, Vetrotex, Menzolit i Owens-Corning. W zakładach ERCOM działała instalacja do recyklingu mechanicznego kompozytów, pozwalająca na rozdrobnienie i frakcjonowanie ok. 6 tys. ton rocznie. Ze względu jednak na zmienione uwarunkowania prawne po kilku latach zaprzestano produkcji recyklatów.
Współcześnie na znaczeniu zyskał recykling termiczny wyrobów wykonanych z materiałów kompozytowych. Przykładem może być niemieckie rozwiązanie CompoCycle, w którym rozdrabniane kompozyty zastępują surowce używane w cementowni. Proces ten jest diametralnie różny od zwykłego spalania odpadów. W jego wyniku z zawartości nieorganicznej uzyskuje się wartościowy materiał, natomiast termoplastyczna matryca służy jako paliwo.
Jak jednak wskazują badacze, brakuje jak na razie rozwiązania, które mogłoby zaspokoić potrzeby przemysłu, dlatego też naukowcy intensywnie poszukują nowych metod recyklingu kompozytów. Oto kilka z nich.
Naukowcy z Uniwersytetu Technologiczno-Przyrodniczego w Bydgoszczy oraz Uniwersytetu Ekonomicznego w Poznaniu opracowali rozwiązanie w zakresie recyklingu włókna szklanego z kompozytów polimerowo-szklanych; otrzymywane włókno szklane jest następnie używane w kompozytach poliolefinowych. W opracowanej metodzie przetwarzane mogą być wyroby z kompozytów składających się z włókna szklanego oraz polimerów chemoutwardzalnych, zwłaszcza poliestrowych i epoksydowych.
Rozdrobniony kompozyt polimerowo-szklany podgrzewa się do temp. 400-600 st. C w warunkach beztlenowych w atmosferze azotu. Podgrzewanie zachodzi w reaktorze mikrofalowym zaopatrzonym w kontrolę temperatury; po jej ustabilizowaniu wsad jest przetrzymywany do momentu, gdy temperatura zaczyna samoistnie się obniżać. W następnym etapie wsad można rozdrobnić, a następnie podlega on odgazowaniu w temp. 200-250 st. C w czasie od 30 do 120 min. Ogrzewanie w reaktorze prowadzi do dekompozycji matrycy polimerowej, w wyniku czego powstaje ciekła i gazowa frakcja węglowodorowa oraz włókno szklane zmodyfikowane na powierzchni warstwą depozytu węglowego.
Otrzymane w ten sposób włókno szklane może być stosowane do otrzymywania kompozytów z polimerami poliolefinowymi - polietylenem, polipropylenem oraz ich kopolimerami (pierwotnymi lub recyklatami). Uzyskane w ten sposób materiały kompozytowe mogą zawierać 10-80 proc. włókien szklanych i posiadają pożądane właściwości mechaniczne. Charakteryzują się również niskim poziomem wchłaniania wody nawet przy dużym stopniu napełnienia.