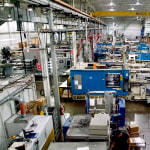
Pod pojęciem zarządzania płynami należy rozumieć wszystkie profilaktyczne przedsięwzięcia odnośnie wyposażenia wtryskarki związanego z pielęgnacją oleju oraz z zakresu kontroli bardzo drobnych zanieczyszczeń, a także nadzór nad tymi przedsięwzięciami podczas całego okresu eksploatacji wtryskarki.
Producent maszyny może stworzyć optymalne podstawy do pielęgnacji oleju, ale ostatecznie to sam przetwórca określa, jakie są tego efekty. Wszystkie elementy konstrukcyjne, a zatem także komponenty systemu filtracji, podlegają zużyciu i należy je okresowo kontrolować pod kątem prawidłowości działania.
Najważniejszym warunkiem utworzenia przynoszącego efekty systemu zarządzania płynami jest rejestrowanie ważnych danych statystycznych.
To o tyle istotne, gdyż w żadnym systemie działań profilaktycznych nie może zabraknąć rejestrowania i dokumentowania takich wartości jak: godziny pracy przy wymianie oleju, godziny pracy przy wymianie filtrów, godziny pracy przy pomiarach klas czystości, godziny pracy przy wymianie pomp, silników hydrostatycznych oraz zaworów proporcjonalnych.
Dokumentacja prowadzona zgodnie z normą ISO 9001 pomaga już przy przeglądzie danych rozpoznawać, które maszyny „źle się spisują” i gdzie należy w przyszłości oczekiwać wystąpienia problemów. Dokumentacja stanowi więc podstawowy warunek rozpoznawania koniecznych przedsięwzięć z zakresu pielęgnacji oleju.
W przypadku czystych układów hydraulicznych o przeciętnej klasie czystości 15/12/09 i lepszej istnieje duże wyprzedzenie czasowe. Tym samym więc nawet przy pomiarach dokonywanych co około 7 tys. godzin pracy można wcześnie zauważyć odchylenia od pożądanej klasy czystości. Oczywiście zakładając, że nie dochodzi przy tym do totalnej awarii komponentu układu hydraulicznego z następującym po niej krótkotrwałym, mocnym wzrostem zanieczyszczenia.
Trzeba koniecznie pamiętać, że przy wystąpieniu większych problemów w układzie hydraulicznym wtryskarki zaleca się natychmiastowe przeprowadzenie pomiaru, aby na podstawie stanu zanieczyszczenia stwierdzić przyczynę zakłócenia lub następstwa awarii komponentu układu.
Główną przyczyną ponad 80 proc. awarii w układzie hydraulicznym jest zanieczyszczenie oleju hydraulicznego.
Wobec tego zadaniem systemu zarządzania płynami jest, aby przy nagłych awariach wtryskarek rejestrować także przyczyny wzrastającego zanieczyszczenia. Jednak w większości przypadków po wymianie uszkodzonego elementu konstrukcyjnego użytkownik zaprzestaje poszukiwania błędów. W ten sposób traci się szansę na wykrycie dalszych ukrytych błędów (np. pęknięte elementy filtracyjne) występujących przy ewentualnym wzroście ilości zanieczyszczeń w układzie.
Wadą zwiększonej ilości zanieczyszczeń bardzo drobnych w układzie jest to, że elementy konstrukcyjne nie ulegają awarii natychmiast, lecz ich uszkodzenia pojawiają się dopiero pod wpływem długotrwałego oddziaływania zanieczyszczeń. Przy zakłóceniach występujących po upływie długiego czasu nie zawsze udaje się już rozpoznać wpływ zużycia spowodowanego zanieczyszczeniem.
Na koniec warto zaznaczyć, że kontrolowanie zanieczyszczeń bardzo drobnych połączone ze znajomością możliwości wczesnego reagowania przed wystąpieniem uszkodzeń może być wykorzystywane jako główna pomoc w utrzymywaniu maszyn do przetwórstwa tworzyw sztucznych w dobrym stanie.