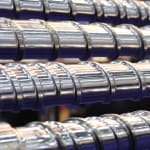
Pierwsza odsłona tego trzyczęściowego cyklu artykułów omawia podstawy doboru właściwego zespołu wtryskowego. Pokazano, w jaki sposób objętość wtrysku wpływa na średnicę ślimaka. Przedstawiono zasady oceny czasu przebywania materiału w cylindrze i wpływ czasu na uszkodzenia termiczne przetwarzanego tworzywa. W końcu przedstawiono wpływ ciśnienia wtrysku i dostępnego dla danej jednostki momentu obrotowego. Całość tych rozważań pozwoli Państwu na optymalne dobranie konstrukcji i wielkości układu uplastyczniającego.
Dla prawidłowego dobrania wtryskarki powinniśmy określić wielkości, które definiują nasze aplikacje. Jednym z najważniejszych dla określenia właściwej maszyny jest dobór układu plastyfikacji. Jednostka uplastyczniająca ma bowiem znaczący wpływ na parametry procesu i jakość uzyskiwanych wyprasek. Na etapie projektowania należy wybrać cechy istotne dla naszej aplikacji. Czasami wybór musi być dokonywany pomiędzy sprzecznymi ze sobą wymaganiami dotyczącymi różnych aplikacji. Należy wtedy określić priorytetowe kryteria. Należy zwrócić uwagę, że np. wybór wykonania układu plastyfikacji o zwiększonej odporności na ścieranie, który związany jest z rodzajem przetwarzanego materiału, nie kończy doboru konstrukcji samego ślimaka. Każdy z dostawców wtryskarek oferuje własne rozwiązania konstrukcyjne dla układów plastykujących.
Może się jednak okazać, że dla konkretnych aplikacji wymagane jest opracowanie ślimaka o specjalnej konstrukcji uwzględniającej nie tylko rodzaj tworzywa, ale także temperatury przetwórstwa, ciśnienia, czy wymagany moment obrotowy napędu ślimaka.
Objętość wtrysku
Jedną z podstawowych wielkości opisujących układ uplastyczniający jest objętość wtrysku. W zależności od przetwarzanego materiału optymalny zakres przetwórstwa wynosi od 1 do 3 średnic ślimaka (D). W przypadku doboru zbyt małego ślimaka dla którego skok dozowania wynosić będzie > 4D możemy spodziewać się pojawienia niestabilności w procesie dozowania. Możliwe będą nie tylko wahania czasu dozowania, ale także zwiększenie stopnia zużycia jednostki uplastyczniającej. Wzrost skoku dozowania prowadzi bowiem do obniżenia efektywnej długości ślimaka. Skrócenie strefy kompresji powoduje, że materiał ma mniej czasu na absorbcję ciepła. Rezultatem jest wzrost ciśnienia w układzie, które niepotrzebnie obciąża tworzywo jak i samą maszynę. Prawidłową objętość wtrysku powinniśmy dobrać wg wzoru:
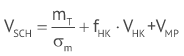
VSCH – objętość wtrysku
mT – ciężar detalu
σm – gęstość materiału
fHK – współczynnik uwzględniający gorące kanały
VHK – objętość gorących kanałów
VMP – wielkość poduszki resztowej
W przypadku układów gorącokanałowych należy uwzględnić kompresję, jakiej ulega uplastyczniony materiał. Układy otwarte i cyklicznie opróżniane, przez które wtryskujemy łatwo płynące tworzywa, będą odznaczać się mniejszą kompresją materiału. Im trudniej płynące tworzywa, im wyższe ciśnienie wtrysku, tym wyższa wartość współczynnika fHK. Wartość tego współczynnika waha się zwykle w przedziale 0,1–0,3.
W przypadku form zimnokanałowych współczynnik fHK jest równy zero. Należy jednak pamiętać, by w formach takich wagę wlewka dodać do wagi wypraski mT.
Trzeba też pamiętać, że objętość poduszki resztkowej materiału VMP powinna zmieniać się wraz ze zmianą średnicy ślimaka:
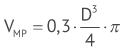
D – średnica ślimaka
Obliczenie objętości wtrysku pozwala na określenie wymaganej średnicy ślimaka. Jak wspomniano wcześniej, skok dozowania powinien zawierać się w przedziale 1 do 3 średnic ślimaka. Mając objętość wtrysku możemy więc określić min. i max. graniczną średnicę ślimaka:
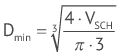
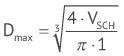
Przy ostatecznym wyborze ślimaka należy uwzględnić wymagania wszystkich planowanych w przyszłości aplikacji i w oparciu o ich analizę wybrać optymalną średnicę ślimaka.
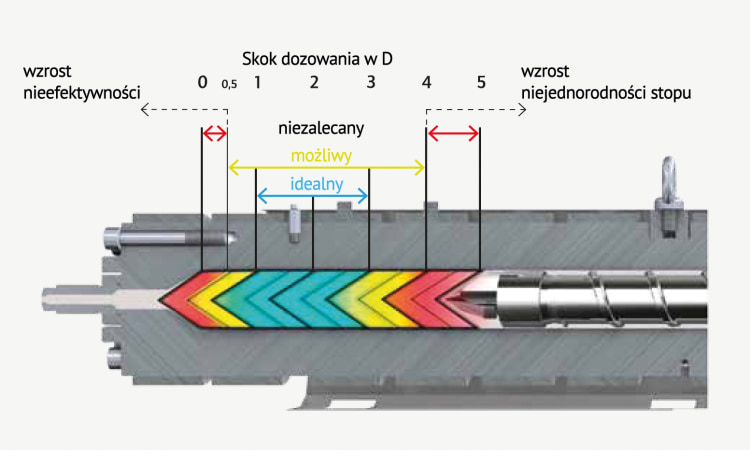
Czas przebywania materiału w cylindrze
Czas, jaki cząstka tworzywa spędza w cylindrze, nazywa się czasem przebywania. Ze względu na złożone procesy przepływu materiału w cylindrze nie da się jednoznacznie określić czasu. Określany jest zwykle przedział, w jakim dany materiał bez uszkodzenia może przebywać w układzie uplastyczniającym. Na rzeczywisty możliwy czas przebywania będą miały wpływ konstrukcja ślimaka, czas cyklu, gęstość nasypowa materiału, gęstość stopu tworzywa oraz parametry procesu takie jak ciśnienie plastyfikacji, prędkość dozowania etc. Tak więc na czas przebywania materiału oddziaływać może każdy z technologów ustawiających parametry procesu.
Przedział czasu przebywania dostarcza informacji o jakości materiału w odniesieniu do stopnia jego mieszania i wystarczającej plastyfikacji. Im szerszy przedział czasu przebywania, tym wyższy efekt mieszania. Obliczanie przedziału czasu przebywania jest jednak dość złożonym zadaniem matematycznym. Dlatego przyjęło się stosować uproszczony sposób określenia czasu przebywania tV dla którego przyjmuje się średni czas przebywania dla typowej cząstki materiału przebywającej w cylindrze układu uplastyczniającego.
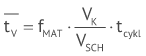
fMAT – korekta gęstości materiału
tcykl – czas cyklu
Współczynnik fMAT uwzględnia różne gęstości materiałów. Sama gęstość ciał stałych jest większa niż gęstość stopu, która z kolei jest większa niż gęstość materiału sypkiego, którą posiada granulowany materiał wyjściowy. Eksperymenty wykazały, że współczynnik ten zwykle wynosi od 0,8 do 0,9.
W przypadku popularnych rodzajów tworzyw sztucznych należy założyć optymalny przedział czasowy od 2 do około 8 minut. Trzeba przyjąć ogólną zasadę, że czas przebywania nie powinien być krótszy niż 1 minuta. Należy wspomnieć jednak, że istnieją duże różnice w stabilności cieplnej poszczególnych tworzyw sztucznych w zależności od dodatków i polimeru podstawowego. Na przykład specjalne rodzaje materiałów stosowane do produkcji soczewek mogą z łatwością przetrwać czasy przebywania powyżej 30 minut. Natomiast tworzywa sztuczne ze środkami medycznymi mogą ulec uszkodzeniu termicznemu już po 2 minutach przebywania w cylindrze.