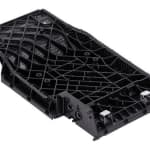
Półprodukty z termoplastycznego materiału kompozytowego Tepex dynalite wzmocnionego ciągłymi włóknami szklanymi znajdują obecnie nowe zastosowania we wnętrzach pojazdów. Jednym z przykładów jest mechanizm składania oparć tylnych siedzeń („load-through”) w pojazdach terenowych wytwarzanych przez europejskiego producenta samochodów. Tylną kanapę wyposażono w mechanizm, który umożliwia składanie oparcia każdego siedzenia oddzielnie. Komponent ten produkuje się poprzez formowanie i wtórne wtryskiwanie materiału Tepex dynalite.
- Wraz z pojawieniem się tej części jesteśmy świadkami wkroczenia materiałów kompozytowych do produkcji lekkich konstrukcji mechanizmów składania oparć tylnych siedzeń. Jest to kolejny dowód na ogromny potencjał tego materiału w produkcji seryjnej - podkreśla Henrik Plaggenborg, szef działu marketingu technicznego i rozwoju biznesowego materiału Tepex w branży samochodowej.
- Nowa część jest o ponad 40% lżejsza niż jej stalowy odpowiednik. Mimo tego ten istotny dla bezpieczeństwa komponent sprawdza się we wszystkich scenariuszach obciążenia, ponieważ ułożenie warstw ciągłych włókien szklanych w półprodukcie o grubości zaledwie dwóch milimetrów zaprojektowano w taki sposób, aby zwiększyć jego odporność na naprężenia mechaniczne - wyjaśnia Harri Dittmar, kierownik projektu i specjalista ds. zastosowań materiału Tepex. Materiał jest produkowany przez Bond-Laminates GmbH, spółkę zależną koncernu LANXESS z siedzibą w Brilonie.
Nowa, lżejsza konstrukcja komponentu została opracowana przez spółkę Brose Fahrzeugteile GmbH & Co. KG przy wsparciu jednostki biznesowej High Performance Materials koncernu LANXESS. Brose wytwarza tę część w swoim zakładzie zlokalizowanym w niemieckim mieście Coburg.
Wytrzymałość przy zderzeniach czołowych i tylnych
Z przyczyn praktycznych system składania oparć montowany jest tylko po jednej stronie, na górnej części oparcia tylnego fotela. Ze względu na umiejscowienie, elementy mechanizmu narażone są na działanie sił zginających i skręcających. Aby mogły wytrzymać takie obciążenia, zdecydowano się na specjalne wieloosiowe ułożenie konstrukcji warstw ciągłych włókien szklanych w termoplastycznym materiale kompozytowym. Materiał Tepex z wieloosiowym wzmocnieniem to kolejna innowacja spółki Bond-Laminates, która sprawia, że arkusze kompozytowe są znacznie wytrzymalsze niż wcześniej. Dzieje się tak dzięki połączeniu materiału Tepex ze wzmocnieniami taśmowymi w wyniku zaawansowanego technologicznie procesu. Półprodukty wykorzystywane do produkcji mechanizmu składania oparć mają budowę trójelementową. Część główna zbudowana jest z czterech warstw, z których każda ma grubość 0,25 mm. Włókna w tych warstwach są ułożone symetrycznie pod kątem +45° i -45° względem podłużnej osi komponentu, dzięki czemu absorbują siły skrętne. Natomiast siły zginające pochłaniane są przez dwie zewnętrzne warstwy, z których każda ma grubość 0,5 mm. W tych warstwach aż 80% włókien ciągłych jest ustawionych w kierunku działania siły. W przypadku zderzenia czołowego takie wieloosiowe ustawienie włókien w warstwach gwarantuje, że nawet tak lekka konstrukcja jest w stanie wytrzymać uderzenie poruszającego się z dużą prędkością ładunku znajdującego się w bagażniku, a w przypadku zderzenia tylnego – siły bezwładności wciskające pasażerów w siedzenia - wyjaśnia Harri Dittmar.
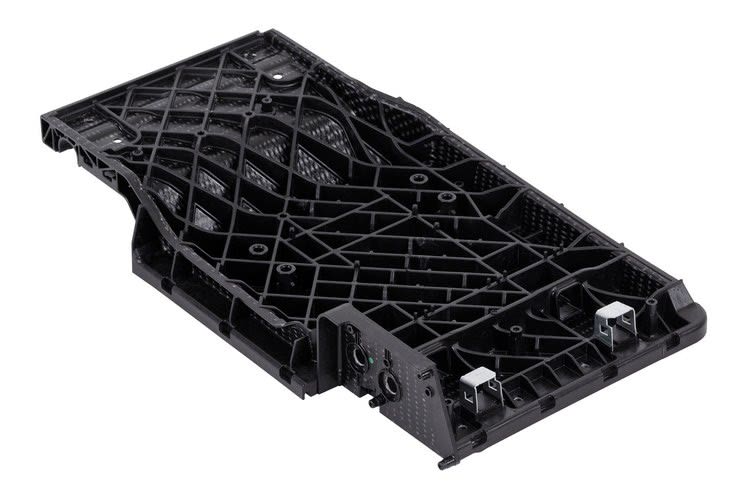