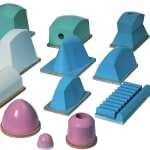
Trzymając w ręku pachnącą farbą drukarską książkę, długopis z nadrukiem reklamowym, czy też kolorowe opakowanie pełne smakowitych czekoladek, mało kto jest świadomy, że do ich wytworzenia potrzebna była guma. Zapewne nie zastanawia się nad tym także wiele osób związanych z przetwórstwem elastomerów…
Guma jest materiałem niezbędnym w wielu gałęziach przemysłu, również w poligrafii, który ze względu na specyficzne właściwości mechaniczne trudno zastąpić. Co więcej, w urządzeniach drukarskich elementy wykonane z elastomerów nie są jedynie częściami napędu, ani nie pełnią wyłącznie funkcji ochronnych, ale wpływają bezpośrednio na proces technologiczny. Z mieszanek kauczukowych wykonuje się m.in. powłoki wałków w maszynach drukujących, obciągi offsetowe, czy grawerowane laserowo drukowe formy fleksograficzne. Od ich jakości i trwałości zależy jakość i efektywność druku przy zastosowaniu takich technik drukarskich jak: tampondruk, offset, czy fleksografia.
Tampondruk
Najprawdopodobniej pozostanie tajemnicą, kto wynalazł tampondruk. Wiadomo jednak, że korzenie tej metody drukowania tkwią w przemyśle zegarmistrzowskim i ceramicznym. Szwajcarscy zegarmistrzowie początkowo zdobili tarcze wytwarzanych przez siebie zegarków za pomocą pędzli, co było czynnością niezwykle czasochłonną. Z biegiem czasu i postępem miniaturyzacji, tarcze zmniejszały się coraz bardziej. Żeby je ozdobić, potrzebne były z kolei coraz mniejsze pędzle. Ostatecznie trzeba było używać pojedynczego włosia i szkła powiększającego – w ten sposób powstawały prawdziwe dzieła sztuki, które można podziwiać w muzeum zegarków w La Chaux de Fonds w Szwajcarii. Pisma stały się tak małe, że nieuzbrojone oko nie było w stanie ich odczytać, a na fantazyjne czasomierze nanoszono nawet fragmenty biblijne i mapy.
Mimo szczegółowych badań zegarków zgromadzonych w La Chaux de Fonds nie udało się ustalić, kiedy nastąpiło przejście na tampondruk; tj. kiedy rozpoczęto mechaniczną reprodukcję z grawerowanej matrycy. Wiadomo jednak, że pierwsze maszyny tampondrukowe były używane już w XVIII w.
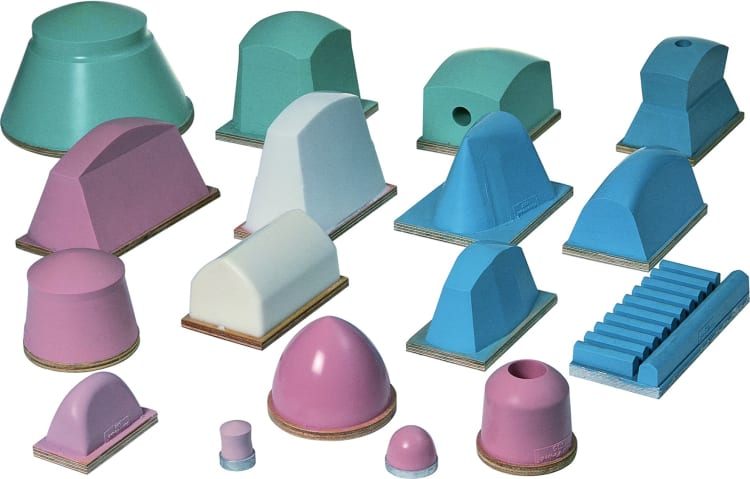
Fot. 1. Tampony silikonowe o różnych kształtach
W tampondruku drukarz wykorzystuje do nakładania farby na podłoże miękkie, gładkie stemple z kauczuku silikonowego, zwane tamponami, które są kluczowym elementem tej techniki druku. Na jakość nadruku wpływa ich kształt, twardość i wykończenie powierzchni.
W tej technice drukowania można nanosić obrazy na rozmaite podłoża, w tym na przedmioty o złożonych kształtach (co doskonale zaobserwować można w branży reklamowej). Tampon może także przybierać kształt rolki (tampondruk rotacyjny) do ciągłego zadrukowywania, np. osłon przewodów elektrycznych lub rur i innych kształtek z tworzyw sztucznych.
Twardość tamponu reguluje się poprzez dodanie zmiękczacza – oleju silikonowego o niskiej lepkości – do mieszanki przed rozpoczęciem sieciowania. Zmieniając stosunek ilościowy olej/kauczuk silikonowy można otrzymać cały typoszereg tamponów różniących się twardością.
Końcowa twardość tamponu jest niezwykle ważna. Jeśli odbiega ona o 4 stopnie Shore A od wartości zakładanej, to uwidaczniają się zmiany w jakości nadruków. Ogólnie, bardziej miękkie tampony są mniej efektywne, jeśli chodzi o przenoszenie farby. Stemple wyprodukowane w niewłaściwy sposób (ze źle skomponowanej mieszanki) będą twardnieć w czasie, co również nie pozostanie bez wpływu na jakość nadruków. Jeśli materiał z którego wykonano tampon jest zbyt twardy, nie odkształca się odpowiednio i nie odwzorowuje właściwie obrazu; ponadto uszkodzeniu może ulec obiekt, na który nanoszony jest nadruk.
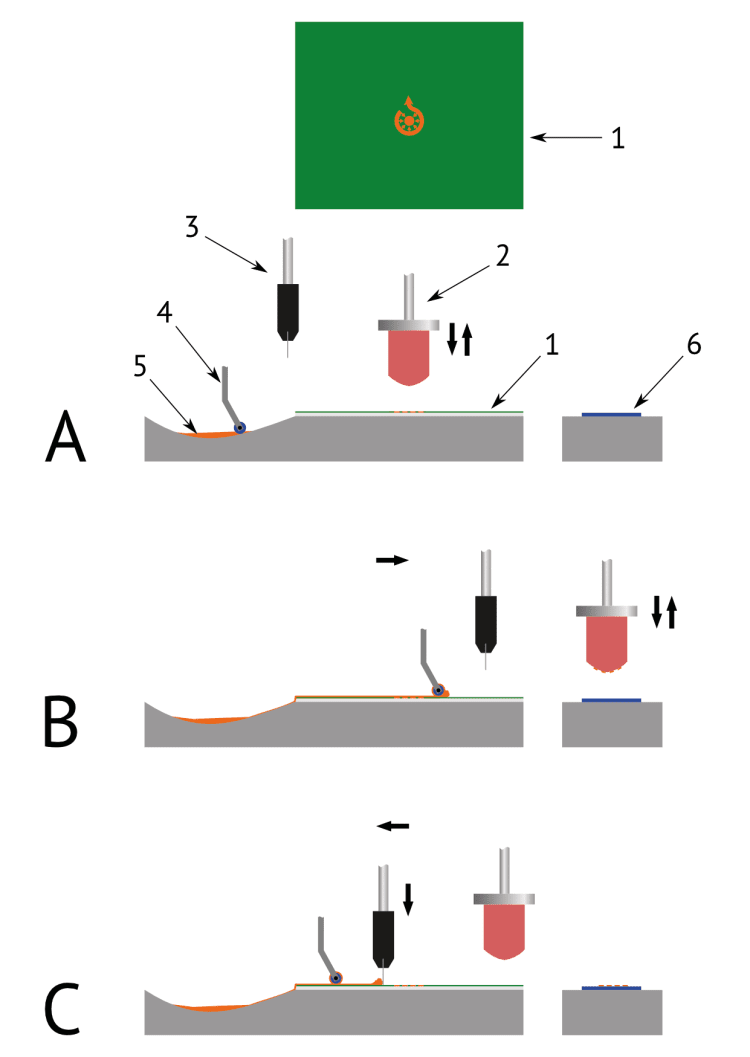
Rys. 1. Schemat urządzenia do tampondruku (tamponiarki) oraz poszczególne etapy drukowania tą techniką: 1 – matryca, 2 – tampon, 3 – rakiel, 4 – nagarniak, 5 – farba, 6 – podłoże drukowe; A – nakładanie farby na tampon, B – nagarnianie farby na matrycę i drukowanie, C – zgarnianie nadmiaru farby z matrycy
Producent tamponów najczęściej dokonuje doboru silikonu kierując się indywidualnymi potrzebami klienta. Każdy z użytkowników posługuje się bowiem unikalną kompozycją farby – zawartością procentową opóźniacza, rozcieńczalników, dodatków antystatycznych, promotorów adhezji i utwardzacza, w zależności od rodzaju zadrukowywanej powierzchni. Możemy posługiwać się silikonem, który jest niepolarny i doskonale nadaje się do farb, opóźniaczy na bazie rozcieńczalników organicznych. Do niepolarnego kauczuku silikonowego można wprowadzić więcej zmiękczacza i uzyskać bardziej miękkie tampony. Możemy też zastosować silikon, który po usieciowaniu będzie charakteryzował się bardziej polarną powierzchnią i który będzie bardziej odporny na działanie kompozycji drukarskich na bazie rozpuszczalników polarnych, np. alkoholi.
Zazwyczaj wykorzystuje się tampony o twardości z zakresu 2–18 Shore A, jednak w specjalnych zastosowaniach zakres ten wynosi 0–40 Shore A. Twardszy tampon lepiej odwzorowuje elementy dekoracyjne i ma dłuższą żywotność ze względu na większą stabilność właściwości mechanicznych. Jednak w wielu przypadkach pożądana twardość nie może być zastosowana, ponieważ uszkodzeniu mógłby ulec zadrukowywany materiał. Bardziej miękkie tampony używane są do nierównych lub złożonych powierzchni, ponieważ dostosowują się do nich lepiej niż tampony twarde. Wybór rodzaju tamponu uzależniony jest od właściwości urządzenia.
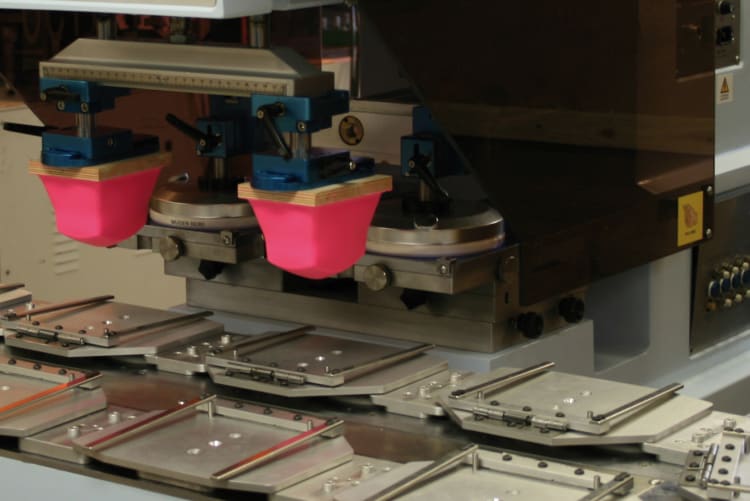
Fot. 2. Fragment tamponiarki z widocznymi stemplami silikonowymi
Przygotowanie stempli silikonowych jest stosunkowo proste. Do ich produkcji potrzebne są formy wykonane z tworzywa sztucznego, wypolerowanego metalu lub żywicy epoksydowej. Receptura materiałowa oparta jest na silikonach dwuskładnikowych RTV sieciowanych na zimno w procesie addycji (katalizatory platynowe) lub kondensacji (katalizatory cynowe). Przygotowanie mieszaniny sieciującej addytywnie polega na wymieszaniu dwóch składników A i B w proporcji 10:1 lub 1:1. Sieciowanie przebiega w temperaturze pokojowej. Aby je przyspieszyć, mieszaninę można ogrzać. Otrzymane stemple mają doskonałe właściwości mechaniczne, relatywnie wysoką twardość (>25 Shore A) i dobrą odporność na działanie rozpuszczalników, dlatego są szczególnie przydatne do farb zawierających agresywnie działające substancje. Silikony sieciujące poprzez kondensację miesza się z katalizatorem w stosunku 20:1. W rezultacie można uzyskać tampony o doskonałych właściwościach mechanicznych w szerokim zakresie twardości, nawet poniżej 1 Shore A. W tym wypadku nie zaleca się stosowania oleju silikonowego jako zmiękczacza, ze względu na skłonność do jego nadmiernego „wypacania się” na powierzchnię stempla w trakcie pracy. Jednak lepsze właściwości fizyczne, takie jak odporność na ścieranie, pęcznienie (pod wpływem rozpuszczalnika), uzyskuje się dla silikonów sieciowanych w reakcji poliaddycji. Są one niestety droższe od tych sieciowanych przez polikondensację.
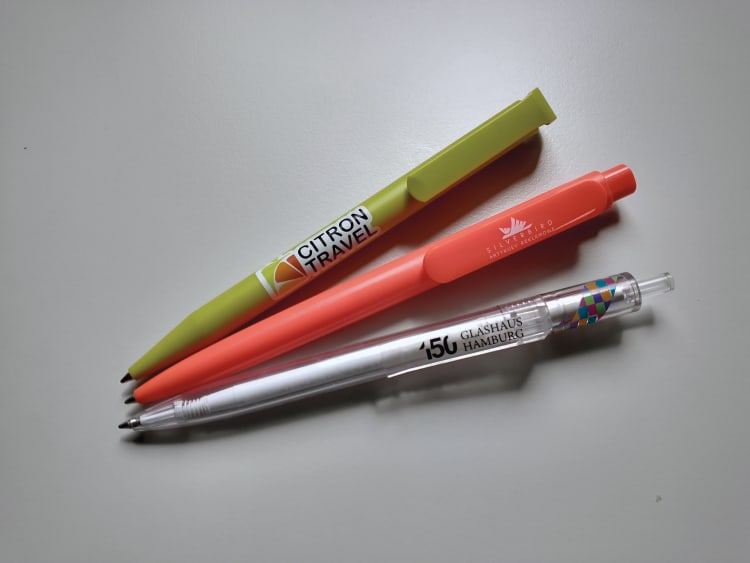
Fot. 3. Artykuły reklamowe z nadrukami wykonanymi techniką tampondruku