Offset
Drukowanie techniką offsetową jest najbardziej rozpowszechnione, zwłaszcza jeśli chodzi o druk wysokich nakładów. Nanoszenie farby w maszynach offsetowych odbywa się w zespole farbowym, który składa się z systemu wałków i cylindrów. Zadaniem wałków jest m.in. pobieranie farby z kałamarza i przenoszenie jej na formę drukową oraz pobieranie roztworu wodnego i zwilżanie nim formy. Dla niewtajemniczonych – w technice offsetowej elementy drukujące i niedrukujące formy znajdują się w tej samej płaszczyźnie, a ich powierzchnie są odpowiednio hydrofobowe i hydrofilowe. Farba pozostaje jedynie w miejscach niezwilżonych roztworem wodnym. Serce zespołu stanowi cylinder pokryty gumą – tzw. obciągiem, który pośredniczy w przeniesieniu wzoru z formy drukowej na podłoże drukowe.
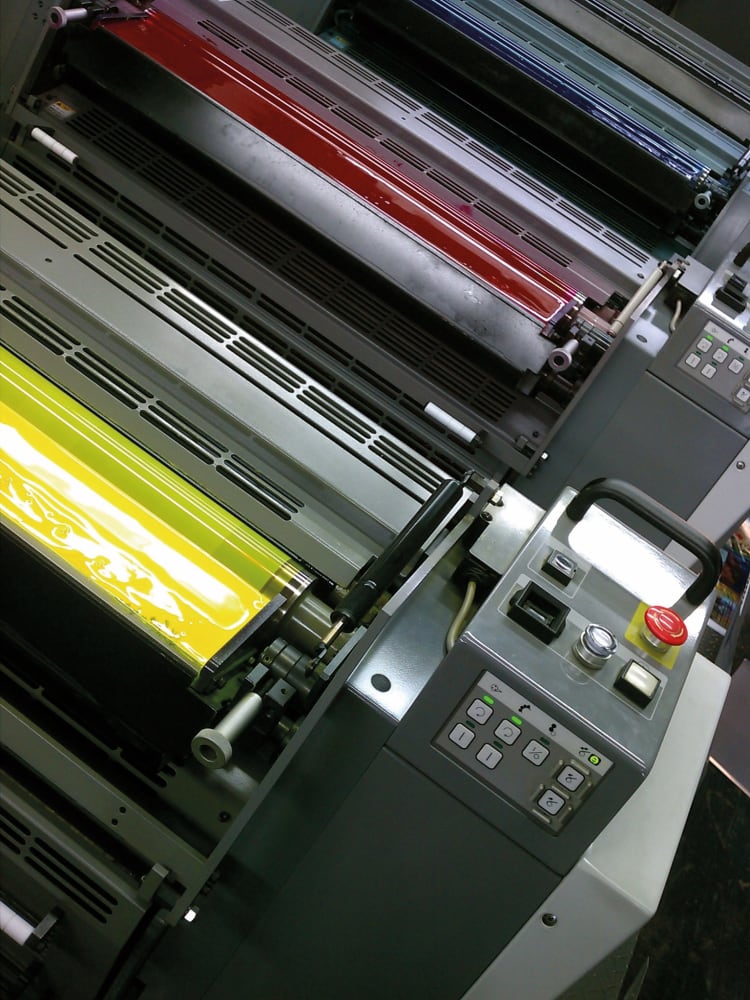
Fot. 5. Maszyna do druku offsetowego
Obciąg offsetowy jest produktem kompozytowym, którego konstrukcję przedstawiono na schemacie (fot. 6). Warstwę wierzchnią stanowi guma, która musi być odporna na działanie roztworu nawilżającego oraz farby, a także na działanie zmywaczy (które często są mieszaniną kilku rozpuszczalników). Pod nią znajduje się tkanina stabilizująca, warstwa kompresyjna oraz kolejne warstwy tkaniny pozwalające na wielokrotne wykorzystanie z zapewnieniem niezbędnego pasowania. Podobnie skonstruowane są płyty lakierujące do lakierowania wybiórczego in-line, w których techniką grawerowania laserowego wycina się pożądany wzór w warstwie gumowej, a zbędny materiał usuwa.
Historycznie ujmując, początkowo wyzwaniem dla producentów wyrobów gumowych na potrzeby poligrafii było sprostanie wymaganiom związanym z odpornością chemiczną materiałów. Obniżenie twardości gumy do 22–35 Shore A wymagało użycia zmiękczaczy, które w wielu przypadkach reagowały z lotnymi związkami organicznymi (VOC), w następstwie czego migrowały z mieszanki. Przez wiele lat problemy związane ze zmianami starzeniowymi gumy – wzrostem twardości, niestabilnością wymiarową – pociągały za sobą znaczne koszty finansowe, które wiązały się z wymianą wałków, a także przestojami na ponowne skalibrowanie maszyn drukarskich.
Kiedy w przemyśle zapoczątkowana została tendencja, aby zaprzestać stosowania lotnych rozpuszczalników organicznych, pojawił się kolejny problem. Okazało się, że nowe rozpuszczalniki powodują pęcznienie gumy, a co więcej, pęcznienie to nie jest równomierne. Miejscowe pęcznienie, zwłaszcza na końcach wałków gumowych, uniemożliwiało operatorom właściwe ustawienie maszyn, a tym samym powodowało błędy druku wynikające z nierównomiernego docisku. Zwiększony docisk zwiększał także ilość ciepła wydzielanego w spęczniałych strefach w trakcie obrotu wałków, co prowadziło ostatecznie do ich przedwczesnego zużycia. Aby zaradzić temu problemowi, producenci wałków wprowadzili nowe rozwiązania konstrukcyjne oraz zmiany recepturowe w mieszankach gumowych.
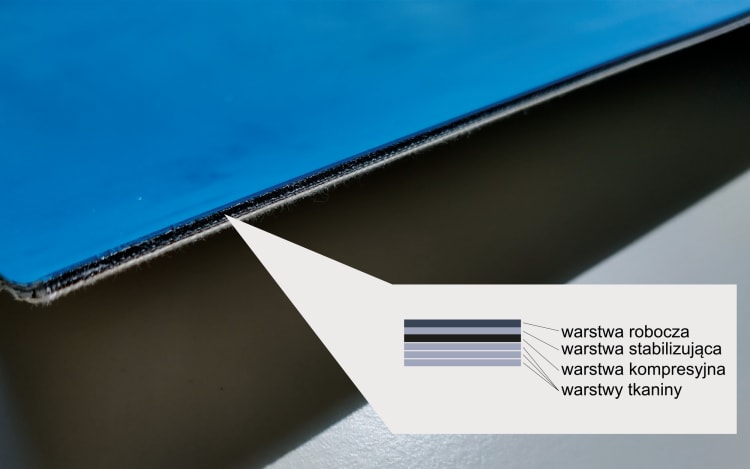
Fot. 6. Offsetowy obciąg elastomerowy w przekroju
Wraz ze wzrostem szybkości drukowania – współczesna arkuszowa maszyna offsetowa może wykonać 18 tys. odbitek formatu B1 w ciągu godziny – zwiększyły się znacznie wymagania dotyczące odporności mechanicznej, m.in. na wielokrotne odkształcenie, i temperaturowej. Dodajmy, że elementy gumowe muszą właściwie spełniać swoją funkcję 24 godziny na dobę, 7 dni w tygodniu, a temperatura pracy waha się w zakresie 27–50°C.
Przykładowo można przyjąć, że rolka gumowa o średnicy ok. 76 milimetrów odkształca się ponad 7500 razy na minutę. Po każdym ściśnięciu musi ona powrócić do stanu pierwotnego w czasie 0,008 sekundy, aby zapewnić właściwe przeniesienie farby. Różnice w średnicy wałka rzędu 0,1 milimetra wynikające z odchyłek produkcyjnych, bądź rozszerzalności cieplnej materiału, mogą powodować nieproporcjonalnie duże zmiany docisku, a tym samym nierównomierne rozprowadzenie farby lub roztworu nawilżającego i negatywnie wpływać na proces druku.
Jak widać na powyższych przykładach, odbiorcy z przemysłu poligraficznego stawiają wysokie wymagania producentom wyrobów gumowych. Elastomerowe elementy drukowe muszą być wykonane z dużą dokładnością i doskonałe jakościowo, aby opakowanie czekoladek czy książka były wykonane estetycznie i spełniły oczekiwania konsumentów.
Dr Karol Niciński