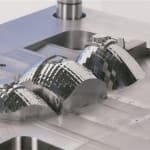
Forma wtryskowa jest narzędziem, które musi sprostać licznym wymaganiom występującym w procesie wtryskiwania tworzyw. Jej najważniejszą funkcją jest umożliwienie wypełnienia płynnym tworzywem gniazd formujących i uformowanie wyrobu, który odzwierciedla kształt gniazd formujących. Jeszcze jednym zadaniem jest skuteczne i równomierne odprowadzanie ciepła od płynnego, gorącego tworzywa. Forma wtryskowa odpowiada także za usuwanie wyprasek w szybki i powtarzalny sposób.
Części formy wtryskowejDo najważniejszych części formy wtryskowej należą:- gniazdo lub gniazda formujące,
- układ wlewowy,
- układ chłodzenia,
- układ wypychania wypraski i wlewka,
- elementy prowadzące i ustalające połówki formy,
- napędy płyt i segmentów jeśli takowe w ogóle występują
- oraz obudowa.
Rodzaje form wtryskowych
Prostym sposobem na wyróżnienie form jest ich podział na zimnokanałowe i gorącokanałowe. Te pierwsze są z reguły tańsze niż gorącokanałowe. Bierze się to z faktu, że zwykle formy zimnokanałowe pozbawione są licznych dodatkowych części, które składają się na system gorącokanałowy i jego osprzęt. W formach zimnokanałowych mamy też do czynienia z większą objętością wtrysku potrzebną do wypełnienia formy w porównaniu do formy gorącokanałowej o tej samej ilości gniazd.
Formy zimnokanałowe
Cechą form zimnokanałowych jest też fakt, że zawsze powstaje tu odpad w postaci wlewka. Wlewek może zostać zmielony, a otrzymany regranulat może być dodany do granulatu jednak w ograniczonych ilościach, tak aby zapewnić wymaganą jakość produktu. W wielu przypadkach niedozwolone jest dodawanie regranulatu.Charakteryzując formy zimnokanałowe trzeba też zaznaczyć, że do ich obsługi wymagana jest większa ilość osób. Decyduje o tym konieczność wykonania pracy związanej z pobraniem wlewków, ich zmieleniem i dodaniem w odpowiedniej ilości do granulatu. To pociąga za sobą oczywiście większe koszty ze zużycie energii elektrycznej. Jest to logiczne, jeśli weźmie się pod uwagę fakt, że ze względu na większą ilość tworzywa potrzebnego w procesie pobierana jest większa ilość energii koniecznej do przeprowadzenia procesu uplastycznienia. Dla małych części masa układu wlewowego może przekroczyć 80 proc. całkowitej masy wtrysku.
Wśród form zimnokanałowych wyróżnia się zazwyczaj formy wtryskowe z jedną płaszczyzną podziału oraz formy wtryskowe z dwiema płaszczyznami podziału (też formy wtryskowe z płytą pływającą).
Czynnikiem decydującym o tym, czy mamy do czynienia z formą z jedną płaszczyzną podziału, czy z dwiema jest przeprowadzenie kanałów wlewowych. Jeśli kanały wlewowe zostały poprowadzone w płaszczyźnie podziału i są usuwane wraz z usuwaniem wyprasek, wtedy forma wtryskowa jest formą z jedną płaszczyzną podziału. Konstrukcja tej formy jest prostsza niż konstrukcja formy z dwiema płaszczyznami podziału. Szczególną popularnością cieszy się zawsze wtedy, gdy możliwe jest zastosowanie którejkolwiek z przewężek krawędziowych. W zależności od rodzaju zastosowanej przewężki wypraska może być oddzielona od wlewka lub nie.
Analizując z kolei formy z dwiema płaszczyznami podziału, zauważyć należy, że kanały doprowadzające tworzywo prowadzone są w dodatkowej płaszczyźnie podziału - potrzebna jest dodatkowa płyta - i z tego choćby powodu forma ta jest nazywana również trójpłytową. W takim przypadku wlewek usuwany jest oddzielnie.
Po formy trójpłytowe sięga się głównie wtedy, gdy konieczne jest doprowadzenie tworzywa do gniazd formujących poza ich krawędzią w płaszczyźnie podziału. Innym powodem ich użycia jest sytuacja, w której użytkownik nie zamierza decydować się na stosowanie formy gorącokanałowej. W przypadku formy trójpłytowej w wyniku usuwania wypraski z formy następuje zawsze oddzielenie wyprasek od wlewka.