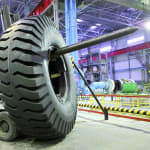
W czasach, gdy energia elektryczna i gaz stają się coraz droższe, warto zastanowić się nad tym, w jaki sposób ograniczyć ich zużycie, tak by zminimalizować ponoszone przez firmę koszty. Kwestia ta dotyczy przedsiębiorstw działających w każdym sektorze przemysłu, a więc także tych reprezentujących branżę gumową.
Koszty energii elektrycznej i gazu rosną, co przy równoczesnym wzroście cen surowców powoduje, że producenci wyrobów z tworzyw sztucznych i gumy zaczynają coraz silniej odczuwać finansową presję - nikt raczej nie zakłada, że w najbliższym czasie tendencje te ulegną zmianie. Oczywiście można potraktować opłaty za energię jako "problem kogoś innego", odpowiednio skalkulować koszty ogólne i stałe, wliczyć je w cenę wyrobów i przerzucić na odbiorców.
Nie o to wszak chodzi, bo postępując w ten sposób ogranicza się konkurencyjność firm na rynku. W rzeczywistości koszty energii są zmienne i można je kontrolować. Dzięki dobrym praktykom zarządzania - chociażby wdrażając normy ISO 14001 i ISO 5001 - można zmniejszyć jej zużycie, uzyskać przewagę rynkową i zwiększyć zyski przedsiębiorstwa. Idealnie byłoby, gdyby polityka energetyczna była częścią szerszej strategii środowiskowej firmy, co przekłada się na korzyści wizerunkowe. Ważne jest też podnoszenie świadomości pracowników w zakresie wprowadzanych programów oszczędzania energii, które powinny być promowane wewnątrz firmy.
Jak to zwykle bywa, zanim firma stanie się energooszczędna trzeba zebrać informacje odnośnie do bieżącego zapotrzebowania na energię oraz dowiedzieć się gdzie, kiedy, dlaczego i ile się jej zużywa. Wiąże się to z poniesieniem kosztów inwestycyjnych związanych chociażby z ustaleniem stosownych punktów odniesienia, audytami energetycznymi oraz opracowaniem i wdrożeniem planów oszczędnościowych.
Przed wykonaniem audytu energetycznego zaleca się sporządzenie wykazu wszystkich głównych urządzeń zużywających energię. Wykaz może mieć postać schematu blokowego lub prostej listy. Głównymi odbiornikami energii elektrycznej w przemyśle gumowym są silniki i napędy urządzeń, układy grzewcze, systemy chłodzenia i oświetlenie.
Opłacalne może być zainstalowanie podliczników na poszczególnych stanowiskach pracy, celem obliczenia kosztu energii dla każdej operacji i identyfikacji najbardziej energochłonnych obszarów (oczywiście technolog bez większego problemu, intuicyjnie, wskaże najbardziej energochłonne miejsca, niemniej jednak chodzi o zebranie danych „ilościowych”). Ważne jest także ustalenie ilości energii niezbędnej do ogrzewania, oświetlenia, zasilenia sprężarek i pomp, gdy w ogóle nie ma produkcji – zmiany w tej sferze to pewny sposób na uzyskanie oszczędności. W idealnej sytuacji energia powinna być wykorzystana tylko do wytworzenia dobrych wyrobów, a więc liczy się też efektywność produkcji.
Przy szacowaniu ilości zużywanej energii warto zwrócić uwagę m.in. na stan izolacji termicznej urządzeń, czy występują nieszczelności w systemach przesyłowych (sprężonego powietrza, wody, pary), czy właściwie dobrana jest moc silników zamontowanych w maszynach, czy stanowiska pracy wyposażone są w instrukcje zawierające odpowiednie ustawienia i czy są one wdrażane podczas produkcji.
Wysokie nakłady energetyczne wiążą się z procesem wytwarzania mieszanek kauczukowych zarówno w mieszarkach zamkniętych (mikserach), jak i na walcach. Warto odpowiedzieć sobie na pytania dotyczące tego, w jaki sposób zużywana jest dostarczana energia i jakie jest faktyczne zapotrzebowanie na nią. Odpowiedź na pierwsze pytanie można uzyskać, sporządzając bilans energetyczny. Drugie pytanie wiąże się ze zrozumieniem mechanizmów mieszania i teoretycznych obliczeń.
Jeśli chodzi o bilans energetyczny, to do tej pory łatwiej było go wykonać dla mieszarek zamkniętych, ponieważ w przypadku walcarek proces mieszania wymaga udziału operatora (nie jest zautomatyzowany). Na szczęście obecnie i tutaj z pomocą przychodzą innowacyjne rozwiązania dla Przemysłu 4.0. Drugie pytanie wymaga podejścia naukowego - wyjaśnienia mechanizmów mieszania i obliczenia teoretycznych wymagań energetycznych.
Na przestrzeni lat technolodzy skrupulatnie przeanalizowali proces mieszania w mikserach, co przyniosło m.in. zmiany w konstrukcji napędu, rotorów, układów chłodzenia, uszczelnień przeciwpyłowych. Siłowniki pneumatyczne zastępowane są hydraulicznymi, które pozwalają na bardziej precyzyjną kontrolę położenia stempla dociskowego i ciśnienia w komorze mieszalnika. Szczegóły można znaleźć w specjalistycznych czasopismach naukowych. Najważniejsze, że współczesne miksery łączą niskie zużycie energii z wysoką wydajnością.
Wyposażenie mikserów i walcarek w systemy informatyczne pozwala zbierać dane dotyczące ich kondycji oraz przewidywać wystąpienie usterki. Napędy nowej generacji wyposażone w przetwornice częstotliwości, w połączeniu z pompami hydraulicznymi, pozwalają na pracę urządzeń z optymalną wydajnością niezależnie od obciążenia. Rejestrowane dane zapewniają kontrolę nad powtarzalnością procesu dla poszczególnych cykli produkcyjnych.
Chcąc obniżyć zużycie energii w procesie sporządzania mieszanek kauczukowych, możemy zastosować szereg substancji pomocniczych (ang. processing aids, processing additives, processing promoters) ułatwiających dyspersję i homogenizację składników oraz upraszczających przeprowadzenie kolejnych operacji technologicznych. W odróżnieniu od zmiękczaczy, dodaje się je do mieszanek kauczukowych w stosunkowo małych ilościach. Zazwyczaj są nimi sole metali nienasyconych kwasów tłuszczowych, kompleksy metali, mieszaniny estrów tłuszczowych kwasów, amidów i alkoholi, faktysy (wulkanizowane oleje roślinne) oraz mieszanki żywic węglowodorowych. Gama tego typu produktów dostępnych na rynku jest naprawdę szeroka.