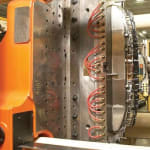
Wiadomo, że poliamid jako materiał semikrystaliczny charakteryzuje się wysokim, zwłaszcza w porównaniu z materiałami amorficznymi, skurczem wypraski. Ogólnie rzecz ujmując na stopień jego krystalizacji, a przez to na wielkość skurczu wpływa szybkość chłodzenia. Czynniki decydujące o szybkości chłodzenia to przede wszystkim grubość ścianek wypraski i temperatura formy.
W niskich temperaturach chłodzenie przebiega szybko i w efekcie stopień krystalizacji zakrzepłego tworzywa jest mniejszy niż w formach o wysokiej temperaturze. Z tej właśnie przyczyny skurcz pierwotny wypraski zwiększa się wraz ze wzrostem temperatury form. Grube detale stygną znacznie wolniej niż cienkie, co jest spowodowane niską przewodnością cieplną tworzyw termoplastycznych, a ostatecznym efektem tego jest mniejszy stopień krystalizacji części cienkich. W związku z tym skurcz wypraski jest tym większy im większa jest jej grubość.
W optymalnej temperaturze formy wskazanej odrębnie dla każdego gatunku tworzywa uzyskuje się optymalny stopień krystalizacji tworzywa. Detale kształtowane w wysokiej temperaturze charakteryzują się niewielkim skurczem całkowitym oraz dobrą stabilnością wymiarową zaś elementy uzyskane w temperaturach niskich wykazują większy skurcz, czasami powodujący powstanie dużych naprężeń wewnętrznych, często prowadzących do przedwczesnego pękania wyrobów.
Czasami przetwarzanie w niskich temperaturach ma na celu podwyższenie wytrzymałości detali, jednakże korzyści uzyskane w ten sposób są niewielkie, gdyż absorpcja wilgoci sama w sobie zwiększa wytrzymałość elementów formowanych wtryskowo. Jeżeli więc formowanie wtryskowe w niskiej temperaturze spowoduje powstanie naprężeń wewnętrznych, to żadne zyski w zakresie wytrzymałości nie zostaną osiągnięte. Dodatkowo kształtowanie w zimnych formach prowadzi do znacznej krystalizacji, a tym samym skurczu, po zakończeniu procesu technologicznego. Wypływa stąd wniosek, że tego rodzaju formowania należy unikać.
Tworzywa poliamidowe wzmocnione włóknem szklanym mogą być wtryskiwane do form o szerokim zakresie temperatur, jednakże najlepszy wygląd powierzchni uzyskuje się w temperaturach wysokich (zazwyczaj 100 st. C – 120 st. C).
Wysokie temperatury form wymagają zastosowania termostatów olejowych lub wodnych ciśnieniowych, ale za to uzyskuje się znacznie lepszą jakość wykończenia powierzchni, poprawia się napełnienie formy oraz maleje ilość wad powierzchniowych (krystaliczność powierzchni).
Jeśli chodzi o czas chłodzenia, to ze względu na krystaliczną charakterystykę tworzyw poliamidowych nie zachodzi potrzeba chłodzenia części po zakończeniu procesu krystalizacji - sztywność wypraski jest na tyle duża, że można ją uwolnić z formy.
Ważną kwestią jest też prędkość obrotowa ślimaka i ciśnienie spiętrzania.
Oto bowiem energia dostarczona przez ślimak powinna stanowić ok. 80 proc. energii niezbędnej do równomiernego podniesienia temperatury (grzałki dostarczają mniejszą część energii). Wynika stąd, że pod uwagę wziąć należy także konstrukcję i charakterystykę pracy ślimaka. Maksymalna sugerowana prędkość obwodowa ślimaka wynosi 0,4 m/s dla poliamidów niewzmocnionych. W przypadku poliamidów wzmocnionych włóknem szklanym prędkość obrotowa ślimaka powinna być niska.
Zaleca się, by prędkość obwodowa ślimaka nie przekraczała 0,15 m/s – pozwoli to ograniczyć do minimum zjawisko pękania włókien szklanych oraz zapobiegnie nadmiernemu zużyciu kanału ślimaka. Zwiększenie prędkości obrotowej ślimaka ogólnego stosowania często kończy się spadkiem temperatury stopionego materiału. Ślimaki o głębokiej i krótkiej części dozującej mogą, przy wysokich prędkościach obrotowych, przetłaczać nieroztopione cząsteczki tworzywa.
Stosować należy niewielkie ciśnienie spiętrzania. Wynikiem jego oddziaływania jest wymuszenie dodatkowej pracy ślimaka, której efektem może być pękanie włókien szklanych i pogorszenie własności mechanicznych gotowego detalu. Wzrost ciśnienia spiętrzania zwiększa wymieszanie stopionego polimeru przez ślimak, a to mogłoby stopniowo podnosić temperaturę i jednorodność stopionego tworzywa. W sytuacji, gdy stopione tworzywo ma niewysoką jakość, wyższe ciśnienie spiętrzania może zmniejszyć zawartość cząsteczek nieroztopionych jednakże nie wpłynie zasadniczo na jakość ciekłego tworzywa.
Zazwyczaj konieczne jest jedynie obniżenie ciśnienia stopionego tworzyw w celu uniknięcia jego wycieku przez dyszę. Dzięki dekompresji uniknąć można wyciekaniu tworzywa z dysz w formach z gorącymi kanałami doprowadzającymi oraz możliwe jest wstrzymanie odgazowania.
Zbyt duże obniżenie ciśnienia może doprowadzić do zassania powietrza przez dyszę, a to z kolei może być przyczyną utlenienia materiału, które następnie objawi się jako odbarwienie wypraski. Innym efektem może być wtryśnięcie zakrzepłego tworzywa w następnym cyklu pracy, prowadzące do powstania defektów powierzchniowych, osłabienia i odchyłek masy wypraski.
Wykorzystano materiały firmy DuPont