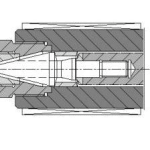
W wtryskarkach przetwarzających tworzywa poliamidowe musi się koniecznie znajdować zawór z pierścieniem zwrotnym (zawór zwrotny), dzięki któremu utrzymać można stałe ciśnienie w formie oraz jednakową masę kolejnych wtrysków. Zawór zwrotny musi być starannie zaprojektowany, z małymi tolerancjami, w taki sposób aby nie utrudniał on przepływu oraz by nie tworzył zbędnych stref zalegania materiału. Musi być o wykonany z odpowiednich gatunków stali odpornej na zużycie.
Jeśli mowa natomiast o zużyciu zawora zwrotnego, to jest on tym elementem zespołu wtryskowego, który jest najbardziej narażonym na zużycie. Zawory zwrotne suwakowe pracujące z tworzywem wzmacnianym włóknem szklanym ulegają szybkiemu i znaczącemu zużyciu w szczególności gdy nie są one właściwie utwardzone. Nawet modele z powierzchniami utwardzonymi zużywają się i wymagają szczegółowej kontroli. Zużyte gniazda i tuleje muszą być wymienione ze względu na znaczenie utrzymania warstwy pośredniej (poduszki) podczas wtryskiwania roztopionego tworzywa. Dobre wyniki można tutaj osiągnąć stosując wysoko wytrzymałe stale chromowe.
Do wtryskiwania wszystkich tworzyw poliamidowych zaleca się również stosowanie otwartych dysz ogrzewanych. Ze względu na większą lepkość roztopionego tworzywa z włóknem szklanym, średnica otworu dyszy stosowanej do wtryskiwania takiego tworzywa powinna być o około jedną czwartą większa niż w przypadku dysz do poliamidów niewzmocnionych. Ze względu na konieczność uniknięcia zarówno degradacji materiału jak i powstawania osadów spowodowanych przez zbyt niską temperaturę bardzo ważne jest nadzorowanie temperatury i właściwe umieszczenie strefy grzewczej.
Zastosowanie dyszy samozamykającej zawsze prowadzi do osadzania się zanieczyszczeń. Ze względu na to, że suwak zaworu ociera się o ściankę zaworu, powstają na nim miejsca, w których gromadzić może się tworzywo. W momencie gdy w miejscach tych nastąpi rozkład tworzywa, ciśnienie może ujść tylko przez tylną część ślimaka, czego efektem są wsteczne wydmuchy materiału.
Ważnym zadaniem jest także kwestia eliminacji stref zalegania tworzywa. Podstawowym celem przy projektowaniu wtryskarki, co obejmuje cylinder grzewczy i elementy przez które przepływa roztopione tworzywo (zawór zwrotny, głowica ślimaka, adapter i dysza) powinno być uzyskanie niezakłóconego przepływu tworzywa.
Szczególnie ważne jest wyeliminowanie wszelkich możliwych i potencjalnych stref zalegania tworzywa, takich jak przylegające do siebie powierzchnie adaptera i cylindra oraz adaptera i dyszy oraz w drugiej kolejności zawór zwrotny lub zawór odcinający w głowicy ślimaka, w miejscu gdzie przylegające do siebie powierzchnie nie mogą być obrobione tak, by uniknąć powstania zagłębień lub miejsc zalegania tworzywa. Z doświadczenia wynika, że jeżeli tylko takie nieprawidłowości występują, to wraz z nimi pojawiają się problemy z zanieczyszczeniem i czarnymi plamami na wyprasce.
Eliminacja możliwych i potencjalnych stref zalegania tworzywa dotyczy też dyszy odcinającej (z zaworem odcinającym), która sprzyja gromadzeniu się zanieczyszczeń, w szczególności podczas pracy z tworzywami wzmocnionymi włóknem szklanym, a ponadto stosowanie takiej dyszy stwarza zagrożenie dla ludzi.
Optymalna konstrukcja przedstawiona jest na poniższym rysunku, który pokazuje zespół składający się z zalecanej dyszy otwartej, adaptera i zaworu zwrotnego. W rozwiązaniu tym powierzchnie styku części znajdują się w złączach walcowych, a ponadto zastosowana jest wtedy dysza otwarta.
Podczas przetwórstwa na wtryskarce tworzyw poliamidowych operator nie musi dodatkowo sprawdzać maszyny, o ile jest ona prawidłowo wybrana i prawidłowo wykorzystywana. Należy jednak zwrócić uwagę na zużycie zaworu zwrotnego, jeżeli do formowania wtryskowego wykorzystywane jest tworzywo zawierające włókno szklane. Cylinder wtryskowy powinien mieć osłonę chroniącą pracowników przed oparzeniem.