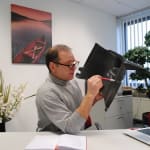
W trakcie słabszego okresu gospodarczego zdroworozsądkowe inwestycje są niezbędne, aby przywrócić konkurencyjność, a także zapewnić firmie przyzwoitą liczbę zamówień. Każdy producent działający w przemyśle tworzyw sztucznych będzie musiał poważnie się zastanowić przed zainwestowaniem w wielokomponentowe maszyny. Dostawca części samochodowych być może zmierzy się z tym samym pytaniem w momencie, kiedy liczba zamówień jest niska a wymagania coraz większe. Być może właściwą odpowiedzią jest przekształcenie jednokomponentnej wtryskarki w wielokomponentową?
Od wielu lat firma Windsor przekształca maszyny jednokomponentowe w wielokomponentowe, oferując szereg atrakcyjnych i opłacalnych rozwiązań. Linia PlugXPress - PxP od 42 do PxP 1780 - to niezależne jednostki wtryskowe, które są w zasadzie odpowiednikami wtryskarek bez układu zamykania. Największą zaletą firmy Windsor jest umiejętność szczególnego dopasowania się do potrzeb klienta. Rezultatem tych działań są indywidualne systemy z odrębnymi specyfikacjami, dzięki którym system PxP łączy się ze wtryskarką poprzez interfejs. Klient nie ma potrzeby dokonywać żadnych modyfikacji w swojej wtryskarce - musi jedynie połączyć system PxP za pomocą śruby w rozmiarze od 16 do 105 mm, kontrolera B&R i 15-calowego ekranu dotykowego. Jednostka PlugXPress dla wielokomponentowych wtryskarek może zostać podłączona do każdego urządzenia.
- Jeden z naszych klientów korzysta z tego rozwiązania przy produkcji szczoteczek do zębów z trzech rożnych tworzyw, w czterech różnych kolorach. Rosnące zapotrzebowanie na urządzenia wielokomponentowe i sukces technologii PxP jest odzwierciedlony w liczbie sprzedanych jednostek w roku 2017, która jest ponad dwa razy większa niż w roku poprzednim. Naszą siłą jest indywidualne dopasowanie do potrzeb klienta, a nasza wysoka elastyczność wyróżnia nas na tle konkurencji. Kiedy standardowe rozwiązania nie zdają egzaminu, PxP przychodzi na ratunek. Jak tylko moduł PxP kończy pracę na jednym zamówieniu, może zostać on podłączony do innej wtryskarki jako moduł przenośny - mówi Andreas Janisch, kierownik produktu w firmie Windsor.
Seria PlugXPress czerpie z rozwiązań typu "plug and play"; jednostki są gotowe do łatwego podłączenia do wtryskarki. Jako niezależny układ uplastyczniający, PxP łączy się z urządzeniem poprzez standardowy interfejs.
- Wszystkie procesy mogą przebiegać w prosty sposób, znacznie usprawniając pracę wtryskarki - podkreśla Janisch. Piękno takiego rozwiązania opiera się na fakcie, że jest ono jednocześnie najwyższej jakości i najnowocześniejsze. Według Janischa w przygotowaniu jest techniczna aktualizacja, które umożliwi kontrolerowi B&R funkcjonowanie poprzez otwarty standard (Open Protocol). Jednostki wtryskowe nie są uproszczone, ale przenośna wtryskarka bez systemu zaciskowego, który pasuje do każdej wtryskarki - jakiegokolwiek typu lub pochodzenia, wtryskuje kolejne komponenty do formy.
- PxP to nie pomniejszona wersja, ale całkowicie funkcjonalne urządzenie. Wysoce odporne na ścieranie materiały to standard. Praktycznie wszystkie istniejące tworzywa termoplastyczne, jak i robione na zamówienie mieszaniny, łącznie z poliamidami zawierającymi włókna szklane i inżynieryjne tworzywa sztuczne mogę być przetwarzane. Oferujemy standardowe trzystrefowe śruby i specjalne dopasowania. W sumie mamy w ofercie dziewięć podstawowych jednostek PxP, z których każda jest wyposażona w trzy ślimaki - dodaje Janisch.
Jak wygląda formowanie wtryskowe przy użyciu PxP? - Po pierwsze, potrzebny jest granulat do pierwszego użycia wtryskarki - w standardowym procesie do podstawowych części - następnie kolejne komponenty poprzez jednostkę PxP - wyjaśnia Janisch. Maszyna sygnalizuje, kiedy granulat jest gotowy. Podczas całego procesu produkty są skrupulatnie rejestrowane. Pamięć PxP jest w stanie pomieścić 1000 programów. Ta liczba może zostać znacznie zwiększona przy użyciu nośnika pamięci USB. Zaletą PxP jest jej możliwość dopasowywania się, która pozwala na oszczędność kosztów producenta. Użytkownik wytwarza części tak, aby zrealizować zamówienie. Z nowym zamówieniem pojawia się kwestia produkowania za pomocą nowych form, szczególnie w przypadku, kiedy mamy do czynienia z produkcją wielokomponentowych części. To sprawia, że pojawia się potrzeba zainwestowania w wielokomponentowe urządzenia. Ale nie jest tak w przypadku PxP: ponosząc koszty w wysokości jednej trzeciej ceny wielokomponentowego urządzenia, użytkownik może unowocześnić swoją standardową jednostkę IMM. Co za tym idzie, zamówienia z którymi wiążą się różne wymagania, są realizowane w bardziej elastyczny sposób. W czasie kryzysu gospodarczego w latach 2008 i 2009 wielu firmom z branży tworzyw sztucznych udało się zanotować znaczące oszczędności dzięki zmodernizowaniu maszyn za pomocą modułów PxP.
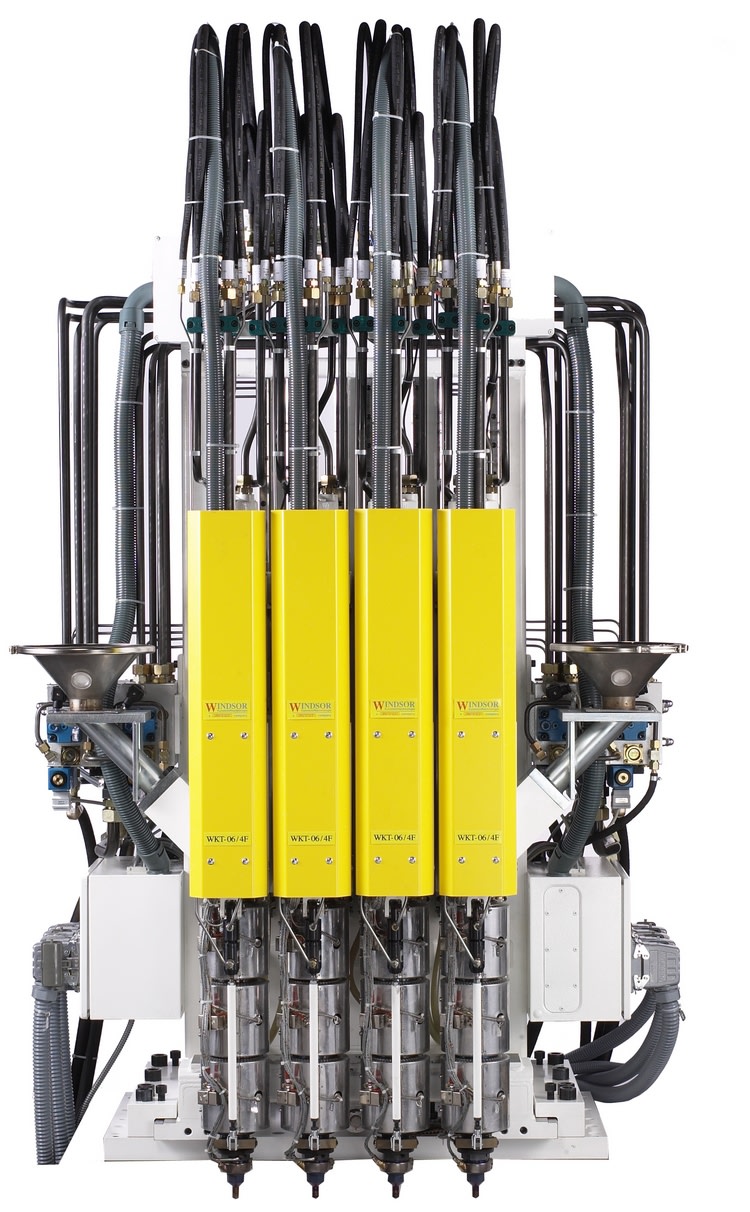