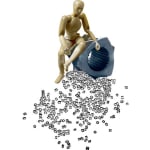
Degradacja może przybrać jedną z dwóch postaci. Po pierwsze może występować jako hydroliza spowodowana wysoką zawartością wody w tworzywie. Druga ewentualność to natomiast degradacja termiczna spowodowana zbyt długim czasem przebywania tworzywa w cylindrze (lub obecnością stref zalegania) bądź nadmierną temperaturą w cylindrze.
Jeśli chodzi o pierwszy wariant, czyli hydrolizę, to jak wiadomo poliamidy są produktami polikondensacji i z tego powodu, w zależności od panującego ciśnienia, wilgotności, temperatury i czasu oddziaływania tych czynników, może dojść do kondesacji lub hydrolizy.
Podczas formowania wtryskowego, masa cząsteczkowa, a zatem i lepkość względna ulegają zmianom zależnym od powyżej wspomnianych parametrów. Podczas formowania wtryskowego tworzywo bardzo suche przechodzi polikondensację, a jego lepkość względna rośnie. Duża wilgotność z kolei prowadzi do zjawiska hydrolizy i spadku lepkości względnej. Stan równowagi, zawartość wilgoci (bez polikondensacji i spadku lepkości względnej) wynosi około 0,12 proc. przy temperaturze masy stopionej wynoszącej 295 st. C.
W momencie, gdy zawartość wilgoci przekroczy 0,25 proc., własności mechaniczne detali formowanych ulegną pogorszeniu, a w szczególności nastąpi spadek wytrzymałości, zmniejszenie wydłużenia, pogorszenie jakości powierzchni oraz będzie łatwo dochodziło do wypływu tworzywa przez dyszę.
Teraz czas na przybliżenie zagadnienia degradacji termicznej.
Podobnie jak wszystkie tworzywa sztuczne, także poliamidy mogą ulec degradacji termicznej. Nie będzie miała ona istotnego znaczenia jeżeli czas przebywania tworzywa w kanale ślimaka nie będzie zbyt długi lub też, gdy temperatura stopionego tworzywa nie będzie zbyt wysoka. W warunkach normalnych szybkość degradacji termicznej jest tak mała, że nie trzeba brać jej pod uwagę.
Jeżeli jednak konieczne jest rozgrzanie stopionego tworzywa do bardzo wysokiej temperatury, np. rzędu 310 st. C, to masa cząsteczkowa tworzywa spadnie np. o 6 proc. przy czasie przebywania 10 minut i o 17 proc. przy czasie 30 minut.
Czas przebywania HUT (Hold-up time) jest średnim czasem potrzebnym na przejście od gardzieli leja do punktu wtrysku formy. Poliamidy, podobnie jak inne tworzywa sztuczne, mogą ulec degradacji podczas procesu formowania. Degradacja polimeru wpływa na masę cząsteczkową i pogarsza jego własności tak, jak to już wyjaśniono powyżej.
Stopień degradacji zależy zarówno od temperatury stopionego tworzywa jak i od czasu przebywania, tzn. od czasu pobytu tworzywa we wtryskarce. Im wyższa jest temperatura ciekłego tworzywa tym krótszy jest czas przebywania po którym dojdzie do degradacji tworzywa. Specjalną uwagę na dobranie optymalnego czasu przebywania HUT należy zwrócić w przypadku tworzyw niepalnych, stabilizowanych cieplnie oraz opracowanych na specjalne potrzeby.
Warto jeszcze skupić się na określeniu charakterystyki stopionego tworzywa przy pomocy form oprzyrządowanych.
Nowy system diagnostyczny wykorzystujący pomiar ciśnienia we wnętrzu formy wtryskowej podczas procesu formowania daje możliwość szybkiego oszacowania bardzo małych zmian charakterystyki tworzywa - płynności i zachowania się podczas krystalizacji, a ponadto pozwala lepiej zrozumieć wpływ różnych parametrów na jakość uzyskanego produktu.
W metodzie tej sygnały analizowane podczas cyklu formowania pochodzą z jednego lub dwóch czujników ciśnienia umieszczonych wewnątrz formy. Komputer mierzy ciśnienie w formie podczas każdego cyklu pracy, przedstawia w postaci graficznej i analizuje.
Wykorzystano m.in. materiały firmy DuPont.