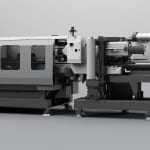
Formowanie wtryskowe jest jednym z najważniejszych procesów masowej produkcji wyrobów z tworzyw termoplastycznych, zwykle bez konieczności dodatkowej obróbki wykończeniowej. Mianem wtryskarki określa się zaś jedno z najważniejszych i najbardziej wielofunkcyjnych narzędzi do produkcji wielkoseryjnej. Obecnie większość urządzeń do formowania wtryskowego to wtryskarki uniwersalne, które w określonych granicach mogą przyjmować wszystkie typy form. Ekonomika tego procesu jest doskonała w przypadku wyrobów o złożonej geometrii, co daje procesowi wtryskiwania przewagę nad innymi technikami.
Sama zasada formowania wtryskowego jest bardzo prosta (co nie oznacza, że sam proces również jest prosty!). Tworzywo sztuczne jest podgrzewane, aż do postaci lepkiego stopu, który jest wtryskiwany pod ciśnieniem do zamkniętej formy, która określa kształt wytwarzanego produktu. Tam materiał jest schładzany, aż powróci do postaci stałej, następnie forma jest otwierana i gotowy element jest z niej wyjmowany.
O procesie wtrysku
Wtrysk tworzyw sztucznych jest procesem coraz częściej stosowanym we wszystkich gałęziach przemysłu. Składają się na to takie czynniki jak:
- ekonomia – proces ten umożliwia pełną automatyzację produkcji wyrobów
- możliwość produkowania przedmiotów o bardzo skomplikowanych kształtach
- proces wtryskiwania prowadzi do stworzenia gotowego wyrobu – powierzchnia nie wymaga obróbki.
Ze względu na specyficzne własności samych tworzyw, wtryskiwanie jest bardzo złożonym procesem technologicznym.
Parametry procesu
Do najważniejszych parametrów procesu wtryskiwania zalicza się: temperaturę, która zależy od temperatury formy, ciśnienia tłoka wtryskowego i szybkości wtrysku; ciśnienie; czas wtrysku, który zależy od wydajności uplastyczniania, ciśnienia oraz temperatury i szybkości wtrysku. Wspomniane parametry decydują o wydajności procesu, jakości wyprasek, własnościach mechanicznych wyrobu i jego zastosowaniu. Dobór tych parametrów zależy od kształtu i wielkości wypraski, rodzaju i własności użytego tworzywa, sprawności pracy wtryskarki.
Zalety
- wytwarzanie skomplikowanych wyrobów w jednym procesie technologicznym
- mały (bądź żaden) udział obróbek wykańczających
- wysoka jakość i powtarzalność właściwości wyrobów
- możliwość pełnego zautomatyzowania, komputerowego sterowania i kontroli procesu.
Wady
- wysoki koszt wtryskarek i niejednokrotnie dorównujący mu koszt oprzyrządowania (form), powodujący wydłużenie czasu amortyzacji i wysokie koszty uruchamiania produkcji
- technologia opłacalna tylko przy produkcji wielkoseryjnej i masowej
- konieczność wysokich kwalifikacji pracowników nadzoru technicznego, którzy muszą znać specyfikę przetwórstwa tworzyw sztucznych
- konieczność zachowania wąskich tolerancji parametrów przetwórstwa
- długi czas przygotowania produkcji ze względu na pracochłonność wykonania form wtryskowych.
Wtryskarki
Ogólna budowa wszystkich typów wtryskarek jest podobna, ponieważ składają się one z pełniących tę samą rolę zespołów funkcyjnych. W zależności od rodzaju przetwarzanego tworzywa, sposobu pracy, rodzaju formy itp., są dostosowywane do wymogów poszczególnych wariantów technologii w sposób konstrukcyjny bądź przez zastosowanie specjalnego wyposażenia technicznego. Wielkość wtryskarki i jej możliwości wytwórcze charakteryzuje siła zamykania, objętość wtrysku i wymiary przestrzeni, w której mocowana jest forma wtryskowa. Przystosowanie wtryskarki do danego tworzywa zazwyczaj odbywa się poprzez drobne zmiany konstrukcyjne lub jej uzbrojenie w dodatkowe elementy wyposażenia. Producenci wtryskarek oferują bardzo szeroki wybór typoszeregu maszyn, które pozwalają na wykonanie założonych zadań.
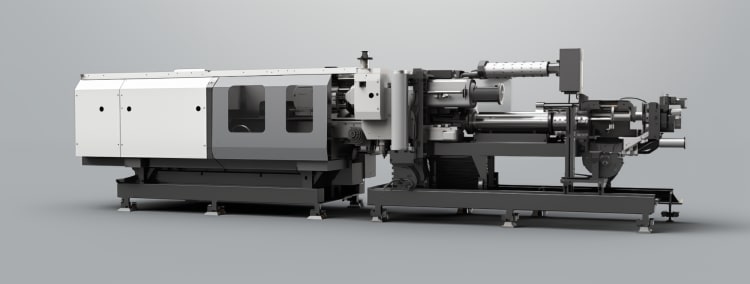
Elementy wtryskarek
Tworzywo sztuczne znajduje się w leju buforowym, z którego przemieszcza się poprzez ruch obrotowy ślimaka w kierunku wtrysku. Sam ślimak podzielony jest z kolei na 3 strefy: pierwszą, gdzie następuje wstępne uplastycznienie tworzywa; drugą, gdzie następuje sprężanie – tworzywo zmienia stan na płynny oraz zostaje spiętrzone; w trzeciej zaś, ostatniej strefie, tworzywo jest homogenizowane. Tutaj już płynne tworzywo zostaje ujednorodnione i jest gotowe do wtrysku. Element wtryskarki, za pomocą którego odbywa się uplastycznienie tworzywa, nazywany jest cylindrem, na którym znajdują się elektryczne elementy grzejne.
Układ wyformowania i zamykania
Po wykonaniu ciekłego wtrysku do formy powstaje wypraska, która następnie zostaje wyformowana poprzez układ wypychania. Wyróżniamy układy mechaniczne, hydrauliczne i pneumatyczne, wykorzystujące do działania wysokie ciśnienie. Samo zamknięcie formy na czas wtrysku realizowane jest poprzez układ zamykania hydraulicznego lub elektrycznego. W zależności od potrzeb produkcyjnych zespół uplastyczniania i wtryskiwania jest wymienny; zwany jest agregatem wtryskowym. Rodzaj budowy tego zespołu określa również nazwę całej wtryskarki.