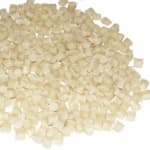
Poliamidy o podwyższonej odporności charakteryzują się nadzwyczaj dobrymi własnościami użytkowymi oraz wysoką dokładnością wymiarową również w wyższych temperaturach. Wykazują odporność chemiczną na działanie olejów silnikowych i transformatorowych oraz glikolu.
Dzięki temu mogą być tańszym zamiennikiem polisiarczku fenylenu (PPS) lub polieteroimidu (PEI) dla wyrobów produkowanych dotychczas z poliamidu 66 lub termoplastycznych poliestrów, a które muszą spełniać wyższe wymagania. Jako przykład można wymienić elementy funkcyjne układu chłodzenia w samochodach.
W przemyśle elektrotechnicznym poliamidy o podwyższonej odporności termicznej stosowane są np. do produkcji elementów konstrukcyjnych oraz narażonych na duże obciążenia termiczne cokołów lamp i korpusów cewek.
Czynnikami przyspieszającymi korozję są długie czasy przebywania stopu w cylindrze, co wiąże się ze stosunkowo niewielką objętością wtrysku, nieproporcjonalnie dużą objętością gorących kanałów, długimi czasami przestoju i obecnością martwych przestrzeni, przy czym martwe przestrzenie są czynnikiem szczególnie krytycznym, gdyż często pozostają niezauważone. Podobnie działają szczeliny lub przestrzenie na wewnętrznych powierzchniach pasowanych stykowo pomiędzy cylindrem uplastyczniającym, łącznikiem i dyszą maszyny oraz niekorzystnie zaprojektowane systemy gorących kanałów.
W układach grzewczych cylindra uplastyczniającego, dyszy maszyny i systemu gorących kanałów należy instalować dobre jakościowo regulatory temperatury, gwarantujące zachowanie nastawionych temperatur z dokładnością plus/minus 3 st. C. Utrzymanie tak dużej dokładności wymaga prawidłowego umiejscowienia czujników temperatury i zastosowania odpowiednio dużej liczby stref regulacji. Cylinder uplastyczniający powinien mieć, co najmniej trzy strefy grzejne odpowiadające strefom funkcyjnym. Izolacje cieplne nie mogą powodować pogorszenia działania regulatorów temperatury.
Zawartość wilgoci w pakowanym fabrycznie granulacie jest mniejsza od 0,2 proc. Materiał ten wchłania wilgoć z otoczenia powoli, ale równocześnie powoli oddaje ją podczas suszenia. Chcąc uzyskać optymalne własności wyrobów należy suszyć granulat w suszarce z nadmuchem suchego, gorącego powietrza przez 4 do 8 godzin w temperaturze 100 st. C, aż do uzyskania resztkowej zawartości wilgoci poniżej 0,1 proc.