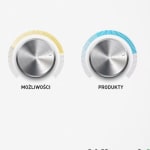
Grudzień to czas podsumowań, również w DRP Group. Tegoroczny bilans dokonań jest wyjątkowy ważny ponieważ firma wysoko zawiesił sobie poprzeczkę na 2017. Czy wszystkie plany udało się zrealizować? – Tak, ale o końcowym efekcie zadecydowało wiele czynników: profesjonalny zespół, odpowiednio przygotowany harmonogram oraz działania, które poprzedziły wdrożenie nowej linii produkcyjnej – mówi prezes firmy Przemysław Miśkiewicz. Najważniejszym dokonaniem jest niewątpliwie rozbudowa i poprawa parku maszynowego poprzez zakup wysoce zaawansowanej linii technologicznej do modyfikacji termoplastycznych tworzyw sztucznych (jest to finalizacja inwestycji dofinansowanej ze środków pochodzących z Unii Europejskiej), ale w bieżącym roku wdrożono również system zarządzania oparty na Lean Manufacturing oraz rozpoczęto wprowadzanie FMEA (Failure mode and effects analysis). Wszystkie te zmiany zadecydowały o jakościowej poprawie finalnego produktu, która idzie w parze z optymalizacją przepływu materiałów i poprawą wydajności na stanowiskach pracy. – W rezultacie otrzymujemy lepsze produkty w bardziej konkurencyjnej cenie – podsumowuje krótko Przemysław Miśkiewicz.
Udoskonalony park maszynowy
Wspominana inwestycja w park maszynowy dotyczy nowej linii do modyfikacji tworzyw sztucznych opartej o wytłaczarkę dwuślimakową. Zastosowane w niej nowoczesne rozwiązania techniczne wpłynęły zarówno na ostateczną jakość, jak i wydajność całego procesu produkcyjnego. Na etapie tak wysokiej specjalizacji znaczenie mają nawet pozornie niewielkie zmiany w budowie urządzeń. Dzięki zbliżeniu kanałów chłodzących i grzewczych do powierzchni cylindra i ślimaków można precyzyjniej zapewnić stałą temperaturę procesu oraz skrócić czas rozruchu urządzeń, zaś modyfikacje w konstrukcji samych ślimaków powodują efektywniejsze uplastycznianie i mieszanie materiałów polimerowych oraz znaczący spadek naprężeń ścinających.Na tym nie koniec. Urządzeniom przeznaczonym do produkcji modyfikowanych gatunków tworzyw i ich konfiguracji stawiane są wysokie wymagania techniczne. Do głównych aspektów tych działań należy zaliczyć:
- Optymalny poziom dyspersji i dystrybucji (właściwa konfiguracja ślimaków)
- Efektywne odgazowanie substancji lotnych (wentylacja atmosferyczna, pompa próżniowa z odgazowaniem umożliwiająca usuwanie substancji lotnych)
- Szeroki zakres prędkości obrotowych ślimaków (wydajność, intensywność mieszania, optymalizacja)
- Wysoki stopień ochrony przed zużyciem (wysoka twardość i trwałość elementów układu plastykującego)
- Precyzyjną regulację parametrów procesu, szczególnie temperatury (umożliwiające jego pełną kontrolę)
- Modułowość budowy ślimaków i cylindra (dostępność, wymienność, ekonomia, ergonomia)
Dzięki zastosowanym innowacjom procesowym w technologii otrzymywania nowych produktów prowadzących do znaczącego ulepszenia obecnych etapów procesu produkcji firma będzie mogła zaoferować szeroką gamę nowych produktów i usług konkurencyjnych nie tylko na polskim ale także na europejskim rynku. Możliwym stanie się także „outsourcingowe” świadczenie usług recompoundingu w oparciu o materiał wtórny powierzony przez kontrahentów dążących do minimalizacji odpadów we własnych zakładach i maksymalizację wykorzystania posiadanych zasobów surowcowych zapewniających efektywność kosztową.