Zapisano cały etap pracy
Proces formowania wtryskowego nadaje tempo drukowaniu wyprasek. Drukowanie musi zostać całkowicie zakończone w czasie cyklu wtrysku. W związku z tym możliwy był tylko bezpośredni proces drukowania, który nie wymaga ani obróbki wstępnej, ani długiego czasu schnięcia. Jeśli chwytak przenosi części natychmiast po wydrukowaniu, wydrukowany obraz nie może się rozmazywać.
Firma Wittmann oceniła wiele procesów drukowania, farb drukarskich i dostawców. Tampodruk został wykluczony ze względu na wymaganą obróbkę wstępną, a niektóre atramenty nie wytrzymały rygorystycznych testów odporności. Przeprowadzono testy wycierania i ścierania przy użyciu różnych rozpuszczalników. Dzieje się tak dlatego, że nawet później używane w opryskiwaczach manometry tłokowe mogą mieć kontakt z agresywnymi mediami, takimi jak pestycydy lub środki czyszczące.
Ostatecznie zdecydowano się na drukarkę atramentową marki Videojet. Zaowocowało to najlepszym wynikiem nie tylko pod względem trwałości farb drukarskich, ale także pod względem elastyczności. - Możemy bardzo precyzyjnie zmieniać położenie drukowanej skali - mówi Sellmayr.
Tendencja do integracji procesów nasila się - Wittmann obserwuje to również wśród innych Przetwórców. W każdym przypadku celem jest optymalne wykorzystanie wydajności poszczególnych komponentów instalacji. W szczególności często robot ma zapas czasu i może przejmować inne zadania podczas wtryskiwania i chłodzenia, takie jak drukowanie na komponentach w Mesto.
- Im więcej zadań robot wykonuje w komórce do formowania wtryskowego, tym mniej wysiłku mamy przy montażu - mówi Élise Sellmayr. - Manometry tłokowe pozostawiają komórkę formowania wtryskowego gotową do montażu. Integrując drukarkę, oszczędzamy cały etap pracy. A co za tym idzie dodatkowy duży wysiłek logistyczny. Dzieje się tak, ponieważ manometry tłokowe były początkowo składane w magazynie i zwykle drukowane w późniejszym terminie.
Zużycie energii zmniejszone o jedną trzecią
Wtryskarki SmartPower dominują w parku maszynowym firmy Mesto. Odkąd w 2017 roku firma uruchomiła kompleksowy projekt mający na celu zwiększenie efektywności energetycznej, stare wtryskarki są konsekwentnie zastępowane przez serwohydrauliczne maszyny SmartPower. Decydującym czynnikiem dla wymiany parku maszynowego była wysoka efektywność energetyczna wtryskarek Wittmann. - Natychmiast zauważyliśmy oszczędności związane ze zmianą - mówi Élise Sellmayr. - Przy tej samej liczbie maszyn udało nam się do tej pory zmniejszyć zużycie energii elektrycznej o jedną trzecią.
Kolejna zaleta: skupienie się na jednej marce maszyn ułatwia operatorom i ustawiaczom maszyn codzienną pracę. - Wszyscy bardzo dobrze dogadują się z systemem sterowania Wittmann - mówi Sellmayr.
Podczas naszej wycieczki po firmie dotarliśmy do wtryskarki SmartPower 180. Z linii produkcyjnej zjeżdżają pokrywy zbiorników ciśnieniowych, czarne płaskie tarcze z wystającymi ze środka tłoczyskami. W formie 2-gniazdowej pokrywy zbiorników są wtryskiwane bezpośrednio na tłoczyska. Przetwarzany jest polipropylen wzmocniony włóknem szklanym.
Niezwykle kompaktowe rozmieszczenie wszystkich komponentów jest również uderzające w tym gnieździe produkcyjnym. Również w tym przypadku liczy się elastyczność. W tym systemie firma Wittmann zintegrowała z ogólną koncepcją urządzenie podające do obtryskiwania prętów metalowych. Wyzwanie polegało na tym, żeby system obsługiwał różne tłoczyska w zależności od modelu opryskiwacza, z których wszystkie musiały być podawane przez jeden i ten sam magazyn.
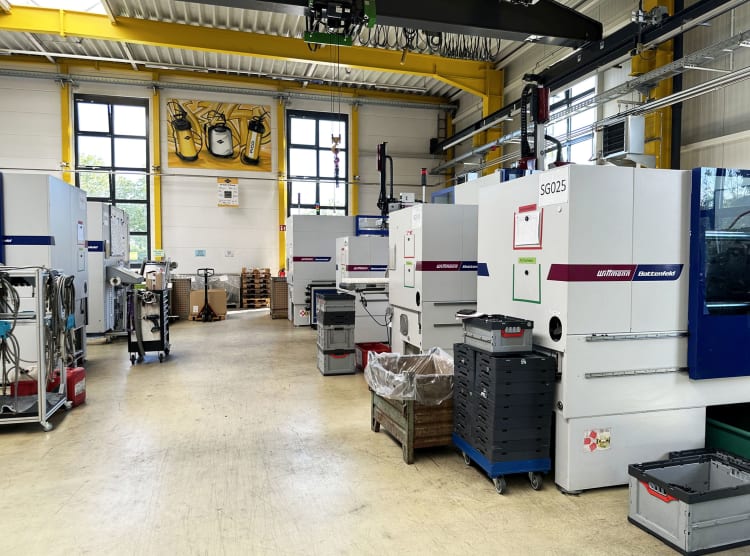
Tłoczyska różnią się między sobą między innymi długością i średnicą. Istnieją pręty obrotowo symetryczne, a także te z latającą i gwintowaną stroną, które należy włożyć w określonej pozycji. Ponadto zmienia się materiał pręta, a tym samym zachowanie magnetyczne.
Wszystkie te aspekty musiały zostać wzięte pod uwagę podczas projektowania chwytaka. Co gorsza, wkładanie metalowych prętów i wyjmowanie gotowych części odbywa się po tej samej stronie narzędzia. W związku z tym chwytak musi łączyć całą funkcjonalność tylko z jednej strony i musi to robić bardzo kompaktowo, aby nadal móc bezpiecznie pracować w otwartym narzędziu.
We wszystkich rozważaniach dotyczących konstrukcji chwytaka, rozmiar i złożoność powstałego chwytaka oraz wydajność produkcji były ze sobą porównywane. W rezultacie, wszystkie wymagania można było połączyć na dwóch chwytakach. Wymiana chwytaka jest całkowicie zautomatyzowana.
Ostatecznym celem we wszystkich projektach jest skończenie z nadmierną inżynierią! Ponieważ byłoby to sprzeczne z wydajnością, elastycznością i łatwością użytkowania. - Przy każdym nowym projekcie omawiamy z Wittmann, co jest możliwe i jakie są nowe pomysły - podkreśla Élise Sellmayr. - Wtedy wspólnie zastanowimy się, który etap rozbudowy ma sens. W końcu są to wszystkie specjalne maszyny, które buduje się tylko raz. Właśnie to sprawia, że jest to tak ekscytujące.