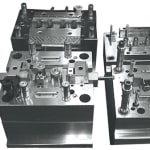
Temperatura formy, a ściślej temperatura powierzchni formy w poszczególnych gniazdach decyduje o tym, jak szybko po wtryśnięciu stopu można będzie odprowadzić wprowadzone wraz z nim ciepło. Regulacja temperatury formy jest niezbędna do rozgrzania formy na początku produkcji i do utrzymywania wymaganej temperatury podczas produkcji.
Jeśli któryś z obszarów formy jest chłodzony silniej niż inne, to wypraska stygnie w tym miejscu szybciej. Następstwem tego są lokalnie większe naprężenia własne, zróżnicowanie skurczu wypraski i paczenie się wypraski po wyjęciu z formy. W przypadku elementów konstrukcyjnych o tolerowanych wymiarach odbija się to niekorzystnie na dokładności wymiarowej.
Warunkiem produkcji wyprasek o dobrej jakości jest równomierne chłodzenie powierzchni formy. Dlatego też otwory chłodzące muszą być rozmieszczone tak, by możliwe było utrzymanie jednolitej temperatury powierzchni formy. Obowiązują tu proste zasady, które jednak niestety często nie są przestrzegane.
W formach na wypraski o zróżnicowanej grubości ścianek otwory chłodzące w obszarach większej grubości ścianek powinny być umieszczone bliżej powierzchni gniazda formy - trzeba stamtąd odprowadzić więcej ciepła - aniżeli w obszarach mniejszej grubości ścianek - w tych miejscach wypraska krzepnie szybciej.
W narożach potrzebne jest chłodzenie szczególnie intensywne, ponieważ kanały chłodzące muszą tam odprowadzać ciepło z dwóch ścianek.
Średnica otworów chłodzących powinna być 2,5 razy większa od grubości ścianki, ale nie może być mniejsza od 5 mm. Z praktyki wynika, że odległość otworów chłodzących od gniazda formy powinna wynosić 2,5 razy tyle co średnica, a w części bocznej trzy razy więcej. Ze względu na konieczność zapewnienia odpowiedniej sztywności mechanicznej formy należy przy ciśnieniach wtrysku powyżej 500 bar wykonywać obliczenia wytrzymałości na odkształcenie.
W dużych formach należy układ regulacji temperatury dzielić na kilka obwodów. W przeciwnym razie chłodziwo nagrzewa się tak mocno, że przy końcu obiegu chłodzenia temperatura formy jest zawsze zbyt wysoka. Przestrzegając powyższych zasad można zapewnić jednolitą temperaturę powierzchni formy, ale wysokość tej temperatury zależy od przetwarzanego tworzywa.