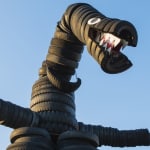
Produkty wykonane z gumy są nieodzowną częścią naszego codziennego życia. Ten niezwykły materiał posiadający jedną niepowtarzalną cechę – elastyczność – znajduje zastosowanie w dziesiątkach tysięcy różnych produktów. Niewiele osób zdaje sobie sprawę z tego, jak bardzo jesteśmy od niego zależni.
Guma kojarzy się nam wszystkim z przemysłem motoryzacyjnym, a ściślej ujmując z oponami. Mało kto jednak wie, że współczesny pojazd oprócz czterech „gumowych” kół kryje w sobie ponad 100 innych elementów (uszczelki, amortyzatory, przewody i złączki spryskiwaczy, wycieraczki, dywaniki, pasy rozrządu itp.) wykonanych z elastomerów. Skojarzenie z oponami samochodowymi jest tak silne, że zapominamy o innych gałęziach transportu – kolei, żegludze, lotnictwie…
Niewielu ludzi jest świadomych, że bez uszczelek i węży wykonanych z elastomerów nie działałby sprzęt gospodarstwa domowego – pralki, zmywarki. Bez elastomerowych podzespołów, często o niewielkich rozmiarach, nie funkcjonowałoby wiele maszyn i urządzeń stosowanych w przemyśle chemicznym, wydobywczym, jak również w rolnictwie, czy medycynie. Bez elastomerów inaczej wyglądałby współczesny sport – zarówno ten wyczynowy, jak i amatorski. Bieganie boso? Pływanie bez czepka? Wędrówki po górach bez wodoodpornych butów? Surfing czy nurkowanie bez neoprenowego kombinezonu? Niby można, ale nie w XXI w.
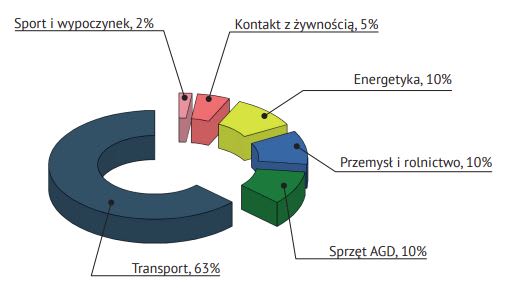
Rys. 1. Główne obszary zastosowań wyrobów gumowych
Zgodnie z danymi publikowanymi przez International Rubber Study Group, całkowita produkcja wyrobów gumowych na świecie w latach 2000–2018, obejmująca zarówno wulkanizaty kauczuku naturalnego, jak i wulkanizaty kauczuków syntetycznych, wzrosła z 17,7 do ponad 29 mln ton. W ostatnich dwóch latach światowe zużycie kauczuków zmalało, częściowo ze względu na eskalację konfliktu handlowego między USA a Chinami w 2019 r. oraz z powodu pandemii COVID-19. Szacuje się, że w 2020 r. światowe zużycie kauczuku naturalnego wyniosło ok. 12,7 mln ton, a kauczuków syntetycznych ok. 14.2 mln ton – co łącznie daje 26,9 mln ton.
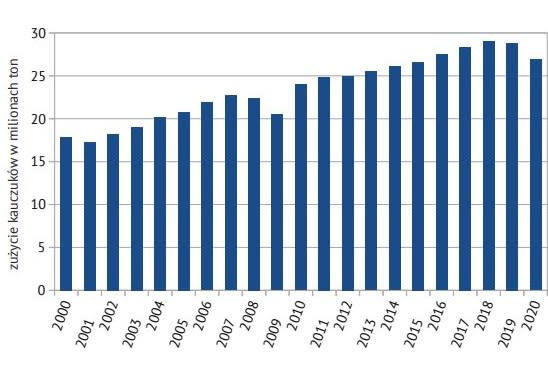
Rys. 2. Światowe zużycie kauczuków w latach 2000–2020
Należy podkreślić, że w przeciwieństwie do produktów wykonanych z papieru, szkła, metali czy tworzyw sztucznych, recykling wyrobów gumowych nie jest sprawą prostą. W skład mieszanki oprócz kauczuku wchodzi bowiem szereg innych surowców – napełniacze aktywne (sadze, krzemionka), napełniacze nieaktywne (kaolin, kreda, litopon itp.), plastyfikatory, środki przeciwstarzeniowe, substancje uniepalniające, zespół wulkanizujący (siarkowy lub nadtlenkowy). W procesie wulkanizacji siarkowej lub nadtlenkowej tworzą się silne wiązania chemiczne, które mają być trwałe i zasadniczo nieodwracalne. W końcu oczekujemy, że wyroby gumowe będą odporne na działanie różnego rodzaju chemikaliów oraz zachowają swoje cechy w szerokim zakresie temperatur przez długi czas.
Recykling gumy staje się tym trudniejszy i bardziej skomplikowany, jeśli uświadomimy sobie, że wulkanizaty mogą być jednorodną mieszaniną różnych kauczuków. W oponach znajdziemy kauczuk naturalny (NR), kauczuk styrenowo-butadienowy (SBR), kauczuk polibutadienowy (BR), kauczuk butylowy (IIR) oraz kopolimery etylenowo-propylenowo-dienowe (EPDM). W pozostałych wyrobach elastomerowych obecnych na rynku, oprócz już wymienionych kauczuków, znajdziemy także kauczuki: nitrylowy (NBR), chloroprenowy (CR), izoprenowy (IR) oraz silikony (MQ, VMQ, PMQ, FVMQ), kopolimery estrów kwasu akrylowego z akrylonitrylem (ACM) czy kauczuki fluorowe (FKM, FPM). Z odpadów gumowych nie odzyskamy w prosty sposób surowców poddając je rozwłóknianiu, jak ma to miejsce w przypadku papieru. Nie przetopimy ich, analogicznie do złomu metalowego czy tworzyw termoplastycznych. Przetworzenie i ponowne wykorzystanie odpadów gumowych jest prawdziwym wyzwaniem.
Historycznie ujmując, pierwszym rozwiązaniem problemu odpadów gumowych była produkcja regeneratu, czyli plastycznego materiału zawierającego wszystkie składniki gumy, z której się go otrzymuje. Jej pionierami w XIX w. byli Thomas Hancock, Aleksander Parkes oraz Charles Goodyear. Regenerat wytwarzano najczęściej trzema metodami:
- olejowo-parową – w której rozdrobnione odpady gumowe miesza się z olejem oraz substancjami zasadowymi (np. wodorotlenkiem sodu), a następnie ogrzewa się w autoklawie, w atmosferze pary wodnej, w temperaturze 190–210°C; częściowo zdewulkanizowany produkt ujednorodnia się poprzez rafinację i/lub filtrowanie
- parową – w której do odpadów gumowych dodaje się jedynie substancje ułatwiające dewulkanizację, a urządzenia wyposażone w elektryczne podgrzewacze wytwarzają przegrzaną parę wodną o temperaturze 230–250°C; szczególnie polecano ją do produkcji regeneratu butylowego
- termiczną – gdzie proces prowadzono w temperaturze 270–290°C.
Za odmianę tej ostatniej metody można uznać późniejszą, termomechaniczną metodę produkcji regeneratu prowadzoną w wysokoobrotowym mikserze o specjalnej konstrukcji lub w sposób ciągły, w urządzeniu typu wytłaczarki. Regenerat dodawano do nowo wytwarzanych mieszanek jako namiastkę droższego kauczuku oraz w celu ułatwienia ich przetwórstwa (kalandrowania, wytłaczania), przy czym zazwyczaj można było nim zastąpić 1/3 kauczuku. Wraz z pojawieniem się na rynku opon radialnych, zmianą procesów technologicznych i niskimi cenami kauczuków SBR i BR, zainteresowanie regeneratem ustało. W latach 80. XX w. wykorzystanie regeneratu oscylowało w granicach 1% światowej produkcji gumy.