Z tego co pan mówi wynika, że narzędziowcy powinni się bardziej kierować względami technicznymi niż kosztowymi.
To jest właśnie clou problemu. Wielu przetwórców uważając, iż dobór układu należy do narzędziowców, daje im w tej kwestii dowolność wyboru i nie łączy własnych problemów z wykorzystywanymi przez siebie systemami. Badania przeprowadzone w 2008 r. przez organizację North America Molders na temat kryteriów zakupu układów gorącokanałowych wykazały, że największe znaczenie dla wtryskowni miała jakość, wydajność, wsparcie techniczne, trwałość, niezawodność, a dopiero na końcu była to cena. Z kolei dla narzędziowni jednym z pierwszych kryteriów była właśnie cena. To pokazuje pewien dysonans i powinno dać sporo do myślenia.
Przetwórcy biorący udział w ankiecie zdawali sobie sprawę z faktu, że gorące kanały mogą mieć dramatyczny wpływ na długoterminowe koszty produkcji. Jeśli układy gorącokanałowe nie pracują poprawnie, wymagają częstych napraw, konserwacji i obsługi, przyczyniając się do obniżenia wydajności gniazda produkcyjnego. Oznacza to, że początkowy wyższy nakład na zastosowanie odpowiedniego układu gorącokanałowego ma sens i nie należy niepotrzebnie oszczędzać. Całkowity koszt okresu użytkowania (ang. Life Cycle Cost) powinien uwzględniać wszystkie koszty, które zostaną poniesione w okresie życia układu g/k, czyli koszty zakupu, koszty operacyjne oraz koszty wycofania z eksploatacji. Niestety bardzo często na etapie budowy formy inwestor rozpatruje jedynie koszty zakupu. A przecież to koszty operacyjne najbardziej wpływają na koszty produkcji. Składają się na nie m.in. czas cyklu, czasy przestoju spowodowane długimi procedurami zmian koloru, napraw, konserwacji, przeglądów, koszt zużycia energii, koszt serwisu i części zamiennych, wreszcie sprawność i wydajność determinujące końcowy odpad produkcyjny.
We wspomnianych badaniach dowiedziono, iż każdy pojedynczy procent zmniejszenia zużycia energii, czy też zredukowania spadków ciśnienia i skrócenia czasu zmiany koloru, w znacznym stopniu wpływa na zmniejszenie kosztów operacyjnych, a co za tym idzie na zwiększenie konkurencyjności.
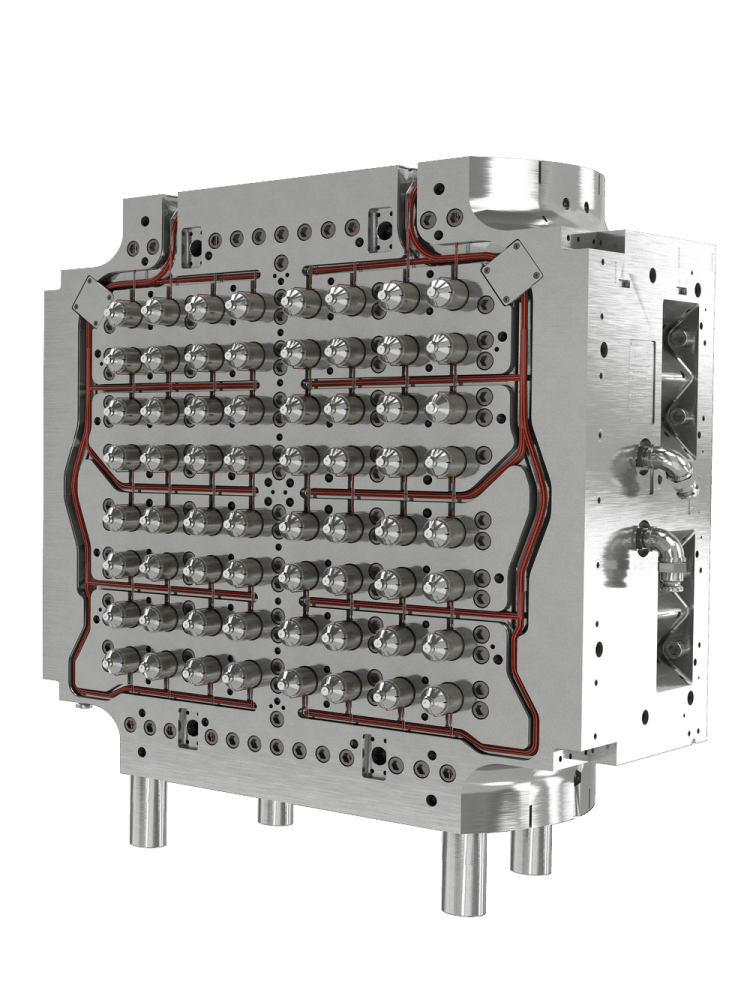
Kompletna gorąca połowa Mold-Masters do formy wielogniazdowej
W zupełnie innych kryteriach postrzegany jest układ g/k przez narzędziownie. W tym przypadku traktowany jest jako jedna z części składowych formy. Wybór dostawcy bardzo często dyktowany jest czynnikami ekonomicznymi, a nie jakościowymi. Niestety sami przetwórcy wymuszają taką sytuację, z góry ograniczając cenę za formę.
Zabawnym jest jednak fakt, iż wybór tak newralgicznego elementu formy jakim jest układ g/k bywa bardzo często zlecany narzędziowni. Wybór układu gorącokanałowego nie powinien być powierzany komuś, kto nigdy nie będzie go użytkował. Oczywiście narzędziownia jest niezbędna do przygotowania specyfikacji układu, czyli podania jego krotności, rozstawów, długości dysz itd., lecz to do wtryskowni powinna należeć decyzja o wyborze. Przyczyny omówiłem wcześniej, ale na etapie powstawania konstrukcji formy, czy nawet samej wypraski niezbędna jest wymiana informacji pomiędzy przetwórcą a dostawcą układu g/k.
Chodzi przede wszystkim o zgromadzenie i wymianę jak największej ilości złych i dobrych doświadczeń z podobnymi wyrobami, sprawdzenie stanu wiedzy zespołu, zaproponowanie najbardziej optymalnego rozwiązania, zapewniającego bezpieczeństwo i niskie koszty produkcji. Oczywiście idealnym przypadkiem jest współpraca trzech stron, czyli wtryskowni, narzędziowni i dostawcy układu g/k. Z niezrozumiałego jednak powodu narzędziownie bardzo często nie dzielą się informacją, kto jest klientem końcowym, a i sami przetwórcy nie widzą potrzeby kontaktu z dostawcą układu g/k.
Chciałbym w tym miejscu wyraźnie zaakcentować, że dobór optymalnego układu g/k gwarantuje wszystkim trzem stronom bezpieczeństwo i stabilność, przez co buduje też relacje biznesowe na poczet przyszłych projektów.
Z naszej rozmowy wynika, że należałoby zmienić hierarchię ważności i postawić formę wyposażoną w układ g/k w roli nadrzędnej. Dziś jest raczej odwrotnie.
Tak, obecnie to wtryskarka najczęściej „dyktuje warunki” formie. Jednak istnieją już urządzenia oraz protokoły zmieniające dotychczasowe reguły gry. Jeśli przyjmiemy, iż to forma jest centrum, a układ g/k jego sercem, to można zapytać w jaki sposób może on kierować całym gniazdem produkcyjnym?
Niedawno wprowadzony standard EUROMAP 83 opiera się na specyfikacji OPC UA. OPC UA jest protokołem komunikacyjnym opracowanym przez OPC Foundation w celu zunifikowania i uproszczenia komunikacji między maszynami oraz peryferiami na ogólnie przyjętych protokołach komunikacyjnych takich jak np. TCP/IP, HTTP, SOAP, co zapewnia dużą skalowalność rozwiązań implementowanych w oparciu o te technologie.
OPC UA od poprzedniej specyfikacji OPC rożni się przede wszystkim tym, iż nie bazuje wyłącznie na technologii COM/DCOM od firmy Microsoft. Komunikację OPC UA można zabudować również do sterowników PLC oraz innych urządzeń. Innymi zaletami nowego interfejsu są przede wszystkim kwestia bezpieczeństwa przechowywania i wymiany danych, konfigurowalne timeouty dla każdej usługi czy w końcu rozdzielenie dużych datagramów na mniejsze części.
OPC UA ma dwoistą naturę, tzn. jest zorientowana obiektowo i usługowo jednocześnie. Natura zorientowana obiektowo powoduje, że protokół OPC UA może być wykorzystywany do wielu celów w warstwie procesowej i zapewnia wsparcie dla zaawansowanych struktur danych oraz elastyczny model danych. Natura zorientowana usługowo zapewnia lepsze wsparcie w dziedzinie przenośności na różnych platformach, lepszy dostęp i bezpieczeństwo. Oznacza to, iż w zasadzie wszystkie parametry układu g/k, które są możliwe do zmierzenia i przetworzenia, są też możliwe do przesłania do innych urządzeń. Pozwala to na wytworzenie środowiska, w którym wszystkie urządzenia wymieniają ze sobą informacje w czasie rzeczywistym, stając się dla siebie równorzędnymi.
Wymiana informacji w czasie rzeczywistym pomiędzy formą, wtryskarką, a innymi peryferiami optymalizuje procesy produkcyjne, znacząco wpływa na ilość odpadu, jak również pozwala na gromadzenie danych niezbędnych do innych analiz czy badań.