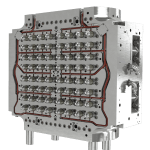
Rozmowa z Piotrem Wieczorkiem, dyrektorem sprzedaży na Europę Wschodnią, Mold-Masters Europa GMBH
Mówi się, że systemy gorącokanałowe zrewolucjonizowały technologię formowania wtryskowego. Jak przebiegała ta rewolucja i dlaczego w ogóle pojawiło się takie rozwiązanie?
Pierwsze wzmianki nt. układów gorącokanałowych pojawiły się już w latach 40. ubiegłego wieku. Do tego czasu przetwórcy byli poniekąd zmuszeni zaakceptować fakt dużej ilości odpadu w postaci wlewków. Niestety pojęcie recyklingu jeszcze nie istniało, więc były one rozpatrywane jako 100% odpad. Bardzo często gałązki wlewka były grubsze, co powodowało bezproduktywne wydłużanie czasu cyklu; poza tym ślad po wlewku był mało satysfakcjonujący i nieestetyczny. Dodatkowo zaobserwowano, iż przechodzenie uplastycznionego tworzywa przez układ zimnych kanałów powodowało straty jego ciepła, co z kolei wpływało na wyższe spadki ciśnienia, a więc m.in. na niedostateczne wypełnienie gniazda formującego. W roku 1940 Knowles opatentował pierwsze rozwiązania mające na celu wyeliminować wspomniane wady. Około 1952 r. firma Protective Closures z Bufallo skonstruowała pierwszą formę z pionierskim systemem gorącokanałowym. Zastosowano wówczas grzaną płytę zintegrowaną z nieruchomym stołem wtryskarki. Nadal jednak zainteresowanie środowiska było niewielkie. Wiązało się to przede wszystkim z ograniczoną możliwością kontroli temperatury i niedoskonałością podstawowych komponentów, takich jak np. termopary. Innym rozwiązaniem pochwaliła się firma Imco około roku 1954. Polegało ono na zastosowaniu „zewnętrznego” układu gorącokanałowego doprowadzającego uplastycznione tworzywo bezpośrednio do gniazda formującego formy.
Do przełomowych osiągnięć należy zaliczyć opatentowanie przez Watlowa elementu grzejnego dla dyszy oraz grzałek patronowych przez Geralda Gilmora, jednego z założycieli firmy Incoe. W roku 1959 narzędziownia Caco-Pacific podobno wyprodukowała w pełni gorącokanałową formę, która zwiększyła wydajność o 107% w porównaniu z konstrukcjami zimnokanałowymi. Wreszcie w roku 1963 firma Mold-Masters opatentowała pierwszy prawdziwie komercyjny system gorącokanałowy. Założyciel firmy Jobst Gellert użył aluminiowych i berylowych elementów dyszy ze zintegrowanym elementem grzejnym, który zapewniał lepszą transmisję ciepła. Jako ciekawostkę podam, iż powszechnie znana z produkcji klocków firma Lego również dorzuciła swój kamyczek do „naszego” ogródka. Na początku lat 60. firma zleciła narzędziowni Schöttli zbudowanie formy eliminującej odpad. Co prawda sam projekt nie okazał się być pełnym sukcesem, lecz zgromadzone doświadczenie pozwoliło na opracowanie własnego rozwiązania, które stosowano w latach 70.
A jak obecnie wygląda rynek układów g/k?
Dzisiejsze układy gorącokanałowe to wysoko wyspecjalizowane rozwiązania pozwalające nie tylko skrócić czas cyklu poprzez eliminację kanałów dolotowych, poprawić kosmetykę detalu oraz jego właściwości mechaniczne, czy w końcu poszerzyć tzw. okno procesowe poprzez precyzyjniejszą kontrolę procesu wtrysku, ale przede wszystkim są one istotnym elementem całego gniazda produkcyjnego, który znacząco może wpływać na obniżenie kosztów produkcji. Szacuje się, że obecnie istnieje około 40 firm produkujących układy gorącokanałowe. Wielu producentów form projektuje własne, dedykowane do swoich konstrukcji układy gorącokanałowe. Niektórzy dostawcy specjalizują się w konkretnych branżach, np. opakowaniowej, automotive czy medycznej. Jednak tylko kilka firm dostarcza rozwiązania dla każdej branży. Są to gracze globalni, posiadający w swoim portfolio rozwiązania w zasadzie dla każdej branży i charakteryzują się dużymi nakładami na badania rozwojowe oraz nowoczesne i innowacyjne technologie.
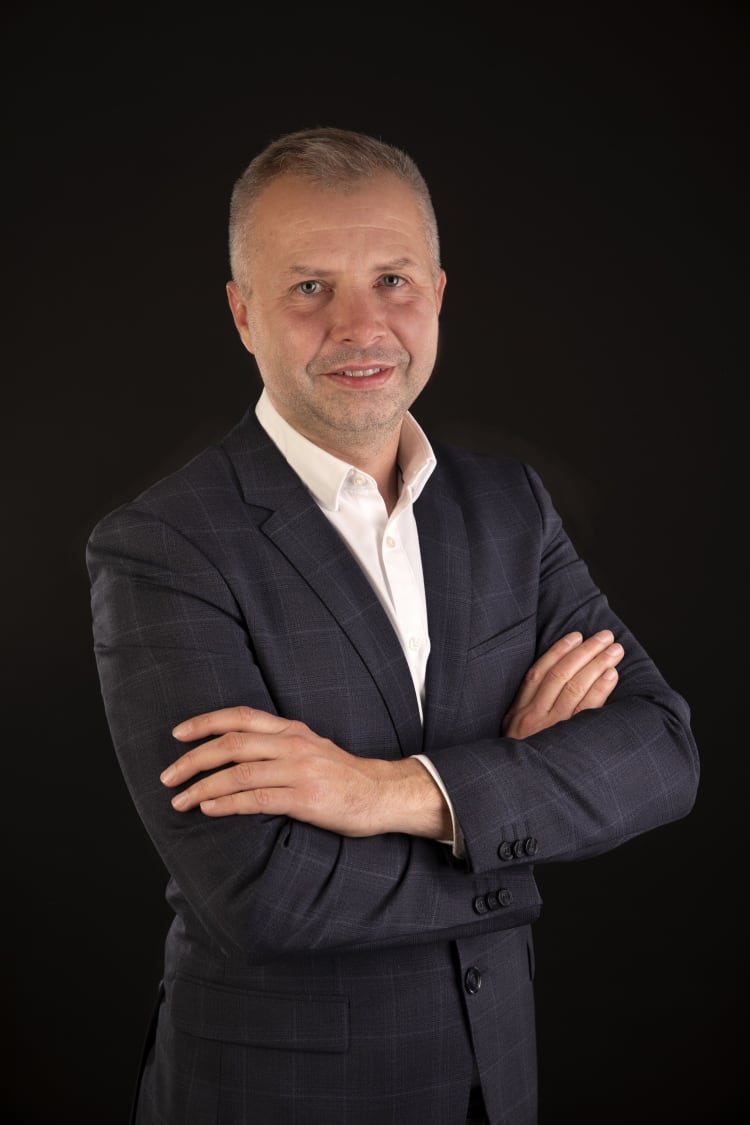
Piotr Wieczorek, dyrektor sprzedaży na Europę Wschodnią, Mold-Masters Europa GMBH
Współczesne systemy gorącokanałowe wykonane są z wysokiej jakości materiałów dobieranych w zależności od przetwarzanego tworzywa; oferują one w zasadzie nieograniczone możliwości dla konstruktora formy. Pozwalają zarówno na wtrysk mikrowyprasek, jak również wyprasek o wadze kilkudziesięciu kilogramów. Tak zwane systemy zamykane iglicowo zapewniają wtrysk z sekwencją, kaskadowy czy synchroniczny. Oferowane napędy bazują na superprecyzyjnych silnikach serwo, dzięki którym w dowolny sposób można profilować skok iglicy czy czas zamykania. Liderzy branży, oprócz układów gorącokanałowych, oferują ultranowoczesne regulatory temperatury (w tym bezprzewodowe) oraz inne peryferia, takie jak np. dodatkowe jednostki wtryskowe. Na rynku są też już obecne rozwiązania wykorzystujące druk 3D.
Jakie są zatem podstawowe zalety stosowania systemów gorącokanałowych?
Na początku trzeba sobie powiedzieć wprost, iż nie wszystkie aplikacje nadają się do przetwórstwa gorącokanałowego. Niektóre tworzywa polimerowe są na tyle wrażliwe, iż bardzo szybko degradują pod wpływem oddziaływań mechanicznych i cieplnych. Wyzwaniem mogą być też aplikacje, gdzie objętość wypraski jest bardzo mała. Jak już wspominałem, współczesne układy gorącokanałowe mają za zadanie obniżyć koszty produkcji oraz zwiększyć elastyczność w automatyzacji produkcji. Profesorowie Demirer, Soydan oraz Kapti z Uniwersytetu Sakaraya w Turcji w swojej publikacji „An experimental investigation of the effects of hot runner system on injection moulding process in comparison with conventional runner system” wykazali, że zastosowanie formy wyposażonej w układ g/k spowodowało redukcję poboru energii, zmniejszenie zapotrzebowania na siłę docisku formy, wydłużenie żywotności formy i wtryskarki oraz poprawiło właściwości mechaniczne wypraski. Do podobnych wniosków doszli panowie Janostik, Stanek, Manas i Senkerik z Uniwersytetu w Zlinie. Efekt ich pracy można prześledzić w artykule „The influence of runner system on production of injection molds”.