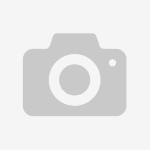
Neopor jest polistyrenem do spieniania (EPS). Nowy zakład może wyprodukować rocznie 90 tys. ton tego tworzywa, przy zastosowaniu nowego procesu opartego na ekstruzji. Właściwości izolacyjne charakteryzujące styropian z Neoporu są aż o 20 proc. lepsze od tradycyjnych materiałów takich, jak Styropor (biały EPS), co prowadzi do oszczędności energii i zmniejszenia emisji dwutlenku węgla.
- Neopor jest materiałem obniżającym zużycie energii oraz koszty budowy i użytkowania budynków, polepszając jednocześnie komfort zamieszkania. Mimo tego, że światowy kryzys finansowy odbija się negatywnie również na sektorze budowlanym, światowy popyt na produkty energooszczędne będzie wzrastał, zarówno w zakresie wtórnego izolowania cieplnego starych budynków jak również chłodzenia budynków - mówi Dr Martin Brudermüller, odpowiedzialny za tworzywa sztuczne w Zarządzie BASF. - Spodziewamy się wzrostu globalnego rynku EPS w sektorze budowlanym o około 5 proc. rocznie w związku z trendem powodowanym rosnącymi cenami energii oraz przepisami prawnymi. W Niemczech około 30 proc. wszystkich materiałów izolacyjnych na bazie EPS wykorzystuje się aktualnie w nowym budownictwie, podczas gdy 70 proc. przypada na projekty renowacji. Do 2012 r. wartość ta ma wzrosnąć do 75 proc.
Srebrzystoszary styropian z Neoporu jest udoskonaloną wersją klasycznego materiału izolacyjnego jakim jest biały styropian ze Styroporu. Zawiera specjalne cząstki grafitu, które odbijają promieniowanie cieplne jak lustro, zmniejszając tym samym straty ciepła w domach. Klienci BASF spieniają granulki Neoporu i przetwarzają je na płyty izolacyjne i elementy formowane (ICF), które następnie są używane do izolacji ścian zewnętrznych, dachów oraz podłóg. Materiały izolacyjne wykonane z Neoporu nie tylko odpowiadają normom budowlanym domu pasywnego, lecz także oszczędzają co najmniej 30 proc. energii koniecznej do ochłodzenia budynków mieszkalnych w ciepłych klimatach.
W odróżnieniu od metody polimeryzacji suspensyjnej (zawiesiny) stosowanej do tej pory, proces ekstruzji w nowym zakładzie pozwoli na uzyskanie granulek o bardziej ujednoliconej wielkości oraz na ustabilizowanie określonych właściwości płyt, np. odporności na ściskanie.
Materiały izolacyjne z Neoporu odgrywają zasadniczą rolę w zmniejszeniu zużycia energii słabo izolowanych do tej pory starych budynków. Np. stary, wielorodzinny budynek mieszkalny zużywa na ogrzewanie 21 litrów oleju opałowego na metr kwadratowy rocznie. Jeżeli poddany zostanie termomodernizacji, w wyniku której zużycie oleju wyniesie tylko 5 litrów, osoby mieszkające w tym budynku w mieszkaniu o powierzchni 80 mkw. zaoszczędzą około 1280 litrów oleju grzewczego rocznie i zmniejszą emisję CO2 o około 4090 kg. Koszty energii koniecznej do wyprodukowania Neoporu na tę izolację – około 1000 litrów oleju opałowego na 80 mkw. powierzchni mieszkalnej – zwracają się już po pierwszym sezonie grzewczym.