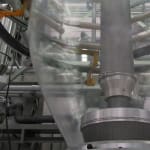
Proces technologiczny wytłaczania polega na ciągłym uplastycznianiu i ujednorodnianiu tworzywa polimerowego w układzie uplastyczniającym wytłaczarki i przetłaczaniu go przez kanały przepływowe głowicy wytłaczarskiej.
Proces uplastyczniania tworzywa polimerowego obejmuje przejście tworzywa wejściowego na skutek nagrzewania i ruchu, ze stanu stałego w stan plastyczny lub plastyczny i ciekły.
Tworzywo wyjściowe musi charakteryzować się określoną temperaturą, ciśnieniem, stopniem wymieszania składu, stopniem ujednorodnienia cieplnego, w tym ujednolicenia historii termomechanicznej i lepkości, oraz natężeniem przepływu. Uplastycznione i ujednorodnione tworzywo jest przetłaczane, często przez zespół filtrujący, do głowicy wytłaczarskiej. Zadaniem głowicy jest ukształtowanie uplastycznionego strumienia tworzywa do wymaganej postaci, np. kształtownika lub rury.
Proces wytłaczania przebiega w wytłaczarkach, gdzie narzędziem jest głowica, przeważnie współpracująca z układem kalibrującym wytłoczynę. Wytłaczarkę tworzy układ uplastyczniający, układ napędowy ślimaka (ślimaków) oraz układ sterowania i regulacji.
Proces uplastyczniania tworzywa polimerowego odbywa się w układzie uplastyczniającym wytłaczarki, który powinien spełniać następujące podstawowe funkcje:
- transportowanie, tj. przemieszczanie tworzywa przez układ z uzyskaniem na jego końcu wymaganej prędkości wypływu w kierunku głowicy,
- nagrzewanie, które prowadzi do zapewnienia zadanego przebiegu zmian stanów fizycznych tworzywa przetwarzanego, określanego temperaturą i jej fluktuacją,
- sprężanie, mające na celu wytworzenie w tworzywie przetwarzanym zadanego przebiegu zmian ciśnienia,
- mieszanie, prowadzone w celu ujednorodnienia składu i właściwości, głównie cieplnych oraz mechanicznych, jak również ujednolicenie właściwości reologicznych przetwarzanego tworzywa.
W celu zwiększenia wydajności wytłaczania, polepszenia jakości wytworów, a zwłaszcza efektywniejszego uplastyczniania tworzyw trudno przetwarzalnych (w tym niestabilnych cieplnie), oprócz wciąż często stosowanych układów jednoślimakowych, stosowane są układy wieloślimakowe - liniowe, planetarne, kaskadowe i inne. Wśród układów wieloślimakowych najszersze zastosowanie znalazły układy dwuślimakowe.
Liczba i różnorodność funkcji układu uplastyczniającego wytłaczarki, które mogą występować w różnych miejscach wzdłuż danego układu powoduje, że zostało opracowanych i praktycznie jest stosowanych wiele rozwiązań konstrukcyjnych tego układu.