Nanoszenie natryskowe
Ta metoda powlekania polega na rozpylaniu i przenoszeniu tworzywa termoplastycznego będącego w stanie ciekłym w strumieniu gazu (zazwyczaj powietrza), w temperaturze normalnej lub nieco podwyższonej, w wyniku czego następuje łączenie tworzywa z nagrzaną powierzchnią przedmiotu powlekanego.
Nanoszenie zanurzeniowe
Nanoszenie zanurzeniowe polega na wprowadzeniu elementu powlekanego w tworzywo powłokowe, będące w stanie ciekłym lub plastycznym, następnie po upływie określonego czasu wyjęciu go i doprowadzeniu powstałej powłoki polimerowej do stanu stałego (utwardzenie powłoki).
Nanoszenie powlekające
Nanoszenie powlekające jest odmianą nanoszenia, w której proces nakładania tworzywa jest ciągły, a tworzywo znajdujące się w stanie ciekłym jest nanoszone na wyroby wykonujące ruch liniowy lub kołowy. Ten rodzaj nanoszenia polimeru wykorzystuje się do dużych lub bardzo dużych elementów. Wyróżnia się nanoszenie powlekające swobodne, w którym tworzywo jest dostarczane bezpośrednio na powierzchnię wytworu, a także nanoszenie powlekające wymuszone, w którym sposób nanoszenia jest ściśle określony i wymuszony różnymi elementami konstrukcyjnymi lub czynnikami technologicznymi. Konstrukcyjnym elementem wymuszającym może być listwa zgarniająca lub układ 2 walców prostych nanoszących. Natomiast technologicznym czynnikiem wymuszającym mogą być kierunki obrotu tych walców (współbieżne lub przeciwbieżne), a także ich prędkość obrotowa.
Nanoszenie płomieniowe
Rozpylanie i przenoszenie sproszkowanego tworzywa termoplastycznego (rzadziej tworzywa będącego w stanie plastycznym) w strumieniu płomienia gorącego gazu i spalin z głowicy natryskującej na powierzchnię wyrobu to nanoszenie płomieniowe. Powierzchnia powlekanego wyrobu musi być nagrzana, aby tworzywo powłokowe uległo stopieniu. Powstanie powłoki jest efektem adhezji cząstek tworzywa z materiałem wyrobu oraz kohezji cząstek tworzywa między sobą. W końcowej fazie procesu następuje ochłodzenie powleczonego elementu oraz ochłodzenie powłoki polimerowej.
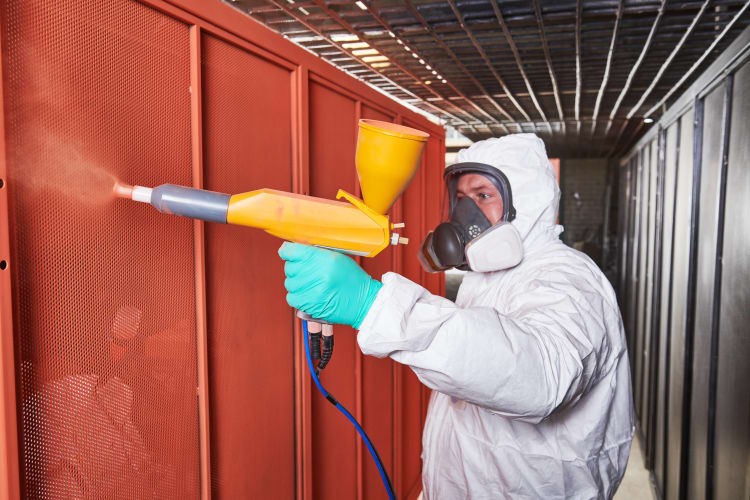
Nanoszenie fluidyzacyjne
Nanoszenie fluidyzacyjne to proces polegający na rozgrzaniu elementu do temperatury nieco powyżej temperatury topnienia tworzywa powłokowego, a następnie zanurzeniu go w złożu fluidalnym, w którym powstaje powłoka polimerowa zestalająca się po wyjęciu przedmiotu z fluidyzatora. Istotą procesu nanoszenia fluidyzacyjnego jest wytworzenie zawiesiny tworzywa w gazie (zawiesinie fluidalnej). Zawiesina fluidalna powstaje, gdy prędkość unoszenia cząstek ciała stałego przez gaz jest równa prędkości ich opadania pod wpływem grawitacji. Cząstki ciała stałego w złożu fluidalnym są w stałym ruchu, przemieszczając się stale po całej objętości naczynia, co sprawia wrażenie, jakby warstwa ta zachowywała się jak wrząca ciecz.
Wytworzenie powłoki metodą nanoszenia fluidyzacyjnego polega na podgrzaniu przedmiotu (np. w piecu komorowym), a następnie natychmiastowym zanurzeniu go w zawiesinie proszku tworzywa w gazie, nazywanej złożem fluidalnym. W złożu fluidalnym następuje przywieranie cząstek tworzywa do gorącej powierzchni przedmiotu powlekanego i topienie się ich. Wygrzanie przedmiotu w komorze powoduje ujednorodnienie stopionej warstwy tworzywa, przez co po ochłodzeniu powstaje trwała, jednolita powłoka.
W metodzie nanoszenia fluidyzacyjnego proces powstawania powłoki można podzielić na 3 etapy:
- powstawanie powłoki jednowarstwowej z cząsteczek tworzywa topiącego się na powierzchni przedmiotu w wyniku bezpośredniego styku z nagrzanym podłożem
- wzrost grubości powłoki w wyniku stopienia się ziaren, które stykają się z już roztopionym tworzywem
- zahamowanie wzrostu grubości powłoki w wyniku utraty ciepła przez przedmiot i małej przewodności cieplnej tworzywa.
Powstawanie zawiesiny proszku w gazie oraz właściwości złoża fluidalnego zależą od wymiarów ziaren, kształtu i gęstości normalnej proszku, prędkości przepływu gazu oraz liczby i średnicy kanalików w porowatym dnie fluidyzatora. Niejednorodność proszku tworzywa może powodować wady złoża fluidalnego, m.in. takie jak pionowe lub poziome rozwarstwienie złoża, segregację faz oraz występowanie w złożu pęcherzy powietrza. Jakość powłoki wytwarzanej metodą fluidyzacyjną zależy od właściwości podłoża, jego cech geometrycznych, grubości przedmiotu, temperatury i czasu jego podgrzewania, a także od czasu zanurzenia przedmiotu w zawiesinie proszku. Tworzywa powłokowe stosowane do nanoszenia fluidyzacyjnego muszą mieć wyłącznie postać proszków, które charakteryzuje się najczęściej określając takie właściwości jak: gęstość nasypowa, wskaźnik szybkości płynięcia oraz wymiary ziarna.
Przykłady stosowania powłok z tworzyw wykonanych metodą nanoszenia to powlekanie nadwozi, podwozi i obręczy kół w przemyśle maszynowym, powlekanie okładzin osłonowych stosowanych w budownictwie, powlekanie szafek szpitalnych, łóżek i wózków oraz wytwarzanie powłok na cysternach, zbiornikach i wieszakach galwanizerskich. Najczęściej nakłada się powłoki z tworzyw sproszkowanych metodą fluidyzacyjną i elektrostatyczną. Powłoki z tworzyw polimerowych wykazują dobrą przyczepność, dobrze zabezpieczają podłoże metalowe przed korozją, mają dobre właściwości izolacyjne elektryczne i cieplne oraz właściwości ślizgowe.