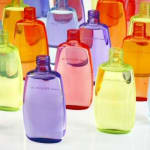
Spheripol jest najpowszechniej stosowaną technologią wytwarzania polipropylenu, jaka kiedykolwiek powstała. W chwili obecnej, proces Spheripol opracowany i wprowadzony na rynek przez firmę Montell, obecnie Basell to efekt ponad 40 lat ciągłego rozwoju technologii wytwarzania poliolefin oraz systemów katalitycznych. Zapewnia on w prosty i dość ekonomiczny sposób wytwarzanie szerokiej gamy polipropylenów najwyższej jakości.
W technologii Spheripol wykorzystywane są bardzo wydajne i mocno selektywne katalizatory, dzięki którym zapewniona jest możliwość produkcji polimeru o kulistych ziarnach bezpośrednio w reaktorze. Tworzące się ziarna polimeru różnią się znacząco od małych cząstek granulatu o nieregularnym kształcie wytwarzanych przy zastosowaniu innych technologii. Różnice te występują przede wszystkim ze względu na bardziej jednorodne warunki przetwarzania tworzywa.
Proces ma charakter modułowy, a typowa konfiguracja składa się z trzech głównych czynników. Pierwszy z ich to zasilanie katalizatorem, drugi polimeryzacja, trzeci zaś końcowa obróbka polimeru. Przy czym trzeba wiedzieć, że mówiąc o polimeryzacji wyróżniamy ją w masie - dla homopolimerów, kopolimerów randomicznych i terpolimerów oraz w fazie gazowej - dla kopolimerów heterofazowych.
Do polimeryzacji w masie stosowany jest charakterystyczny dla tej technologii reaktor pętlowy. Katalizator, ciekły propylen i wodór dla kontroli ciężaru cząsteczkowego są podawane do reaktora w sposób ciągły. Czas przebywania w reaktorze jest krótszy niż w innych technologiach ze względu na wysokie stężenie monomeru i użycie katalizatora o podwyższonej aktywności.
Reaktor pętlowy zapewnia niski koszt procesu, wysoką sprawność cieplną oraz utrzymanie równomiernej temperatury, ciśnienia oraz dystrybucji katalizatora. Krótszy czas oznacza również szybszą zmianę gatunku tworzywa, zaś kompletne wypełnienie reaktora eliminuje ryzyko zanieczyszczenia innymi gatunkami.
Przy produkcji kopolimerów randomicznych lub terpolimerów do reaktora wprowadzane są bardzo niewielkie ilości komonomerów, takich jak etylen i/lub buten-1. Dodatkowo przy produkcji kopolimerów blokowych (tzw. udarowych lub heterofazowych), polimer z pierwszego reaktora pętlowego jest przesyłany do reaktora w fazie gazowej, który pracuje szeregowo z reaktorem pętlowym. Proszek polimerowy z reaktora wpływa do niskociśnieniowego separatora, następnie do zbiornika parowego, gdzie neutralizowane są pozostałości katalizatora, a monomer jest usuwany, odzyskiwany i zawracany do układu reakcyjnego. W finalnym etapie procesu produkt końcowy jest transportowany do zespołu wytłaczania, gdzie jest mieszany z dodatkami i wytłaczany w postaci granulatu.