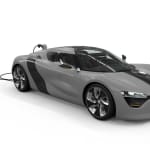
Tworzywa sztuczne sieciowane radiacyjnie: ogromny potencjał dla samochodów elektrycznych - rozmowa z Dr. Michal Daněk, Key Account Manager oddział sieciowania radiacyjnego w spółce BGS
Jak duży jest rynek tworzyw sztucznych sieciowanych radiacyjnie dla przemysłu motoryzacyjnego w Europie Środkowo-Wschodniej i jak rozwijał się on w ostatnich latach?
Całkowita wielkość rynku tworzyw sztucznych sieciowanych radiacyjnie w Europie Środkowo-Wschodniej jest bardzo trudna do oszacowania. Cały rynek ulega ciągłym zmianom, zwłaszcza ze względu na obecne odejście od konwencjonalnych silników spalinowych na rzecz pojazdów w pełni elektrycznych. Niektóre części wykonywane z tworzyw sztucznych sieciowanych radiacyjnie dostępne są wyłącznie do motorów spalinowych, generując zatem wartość dodaną tylko dla tej koncepcji pojazdu. Rynek pojazdów konwencjonalnych rozwijał się w ostatnich latach raczej umiarkowanie. Jednak elektromobilność daje silny nowy impuls do stosowania tworzyw sztucznych sieciowanych radiacyjnie.
Jakie są główne dotychczasowe zastosowania sieciowania radiacyjnego w przemyśle motoryzacyjnym i jakich nowych lub rozszerzonych obszarów zastosowań można się spodziewać w wyniku elektromobilności?
Obecnie tworzywa sztuczne sieciowane radiacyjnie są wykorzystywane głównie w segmencie silników spalinowych i, ogólnie rzecz biorąc, w zastosowaniach wymagających większej odporności na wysokie temperatury, substancje chemiczne lub pełzanie materiału. Przykłady obejmują rury wydechowe, mieszki, elementy mocujące i systemy zasilania (kable). Elektromobilność rozszerza jednak portfolio produktów na kilku poziomach. Z jednej strony obserwować można silnie rosnący popyt na kable, zwłaszcza te wysokonapięciowe. Z drugiej jednak systemy akumulatorowe przedstawiają w pełni nowe obszary zastosowań. Są to na przykład obudowa akumulatora lub same części akumulatorów z tworzywa sztucznego. Tylko użycie części odpornych na ciepło pozwoli na poradzenie sobie z krytycznym stanem obciążeniowym w przypadku „skumulowanego transferu ciepła”. Tworzywa sztuczne sieciowanie radiacyjnie będą odgrywać w tym zakresie coraz istotniejszą rolę.
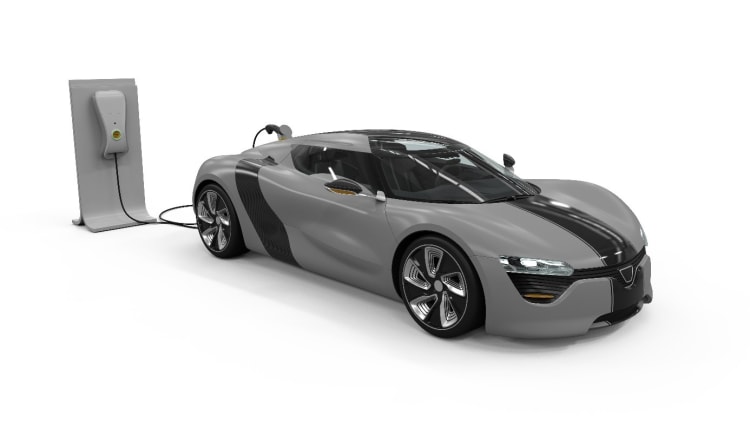
Źródło: BGS Beta-Gamma-Service
Które części lub zespoły w pojeździe powinny być wykonane z tworzyw sztucznych sieciowanych radiacyjnie? Gdzie można je zastąpić metalami, a gdzie wysokowytrzymałymi tworzywami sztucznymi?
Ogólnie rzecz biorąc, wszystkie części i zespoły o podwyższonych wymaganiach w zakresie odporności na temperaturę, substancje chemiczne lub uderzenia są odpowiednimi kandydatami do zastosowania tworzyw sztucznych sieciowanych radiacyjnie. W przypadku niektórych pojazdów metalowe części zewnętrzne zastępowane są tworzywem sztucznym PA66 sieciowanym radiacyjnie z 30-procentową zawartością włókna szklanego. Kolejnym przykładem są elementy mocujące, takie jak nakrętki, śruby lub zaciski wykonywane z tworzywa sztucznego PA66 sieciowanego radiacyjnie zamiast z metalu. Powodem jest niska gęstość czyli niższa waga i lepsze właściwości pod względem wytrzymałości chemicznej. Przykładem zastąpienia wysokowytrzymałych tworzyw sztucznych lub tworzyw sztucznych wzmocnionych włóknem szklanych termoplastycznymi tworzywami sztucznymi sieciowanymi radiacyjnie mogą być styczniki.
Jak duże są oszczędności kosztów w niektórych typowych zastosowaniach w porównaniu z wcześniej używanymi materiałami?
Oszczędności kosztów można osiągnąć na kilka sposobów. Pierwszą opcją jest zastąpienie materiałów, a drugą sama technologia napromieniowania.
Spoczywa ona zawsze w napromieniowaniu „powierzchni”, na której lub pod którą umieszczone są sieciowane radiacyjnie części z tworzywa sztucznego. Posłużmy się przykładem: w tekturowym pudełku o wymiarach 400×400×200 mm zmieści się 1000 zacisków z tworzywa sztucznego sieciowanego radiacyjnie. Oszczędności kosztów można osiągnąć, dzieląc koszty napromieniowania pudełka przez liczbę znajdujących się w nim części. Oznacza to, że koszty na napromieniowanie jednego zacisku są minimalne. Jeśli zaciski pierwotnie wykonywano z metalu lub z tworzywa sztucznego wzmocnionego włóknem szklanym, jego zastąpienie termoplastycznym tworzywem sztucznym sieciowanym radiacyjnie oznacza kolejne oszczędności.
Jaką rolę chce odgrywać spółka BGS w rozwoju w ramach przemysłu motoryzacyjnego i jakie są jej plany w zakresie dalszego rozwoju?
Elektromobilność jest jednym z najszybciej rosnących rynków w dzisiejszych czasach, a spółka BGS zamierza się do tego odpowiednio dostosować. Aktualnie pracujemy nad różnymi projektami rozwojowymi, a także nad projektami typu Start of Production (SOP, rozpoczęcie produkcji seryjnej). Analizujemy również możliwości recyclingu tworzyw sztucznych sieciowanych radiacyjnie. W tej dziedzinie osiągnęliśmy już bardzo dobre wyniki, które staramy się wykorzystać w nowych projektach. Kolejnym obszarem rozwoju jest napromieniowanie półprzewodników mocy do zastosowań w segmentach elektromobilności i energii odnawialnej. Innymi słowy, w ramach wielu zastosowań, w których ważną rolę odgrywa postępująca elektryfikacja. Od kilku lat wykonujemy napromienianie seryjne we wszystkich trzech oddziałach dla szerokiej gamy klientów.